Exploring Heat Simulation Software: A Comprehensive Overview
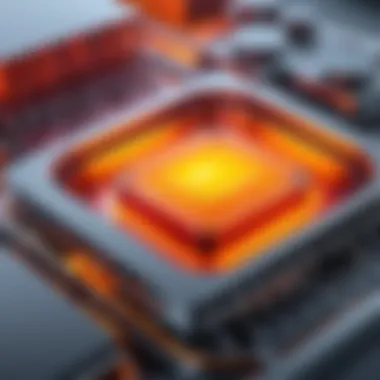
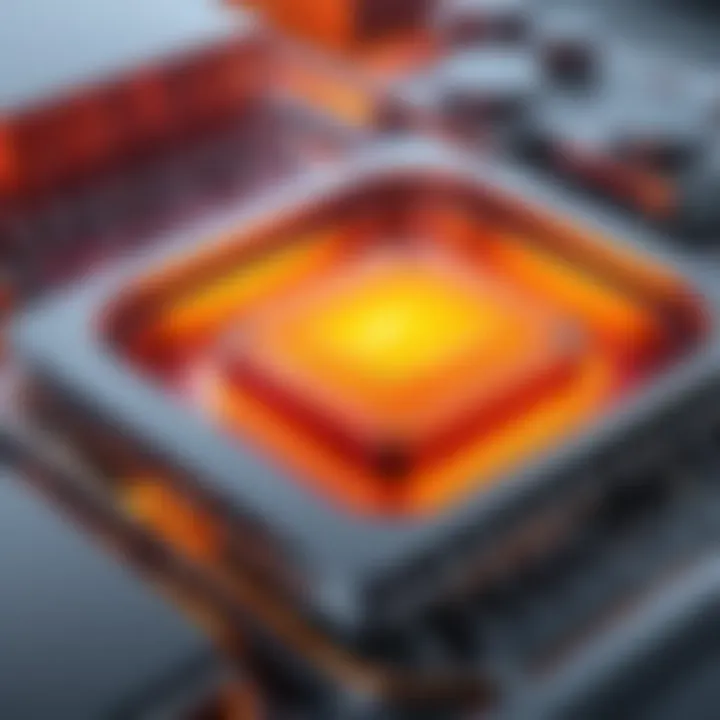
Intro
In today’s world, the ability to simulate heat transfer has become increasingly vital across many sectors. Industries ranging from electronics to aerospace rely on heat simulation software for optimizing designs and processes. The purpose of this article is to provide a structured and detailed exploration of heat simulation software, focusing on its applications, benefits, and challenges.
With the rapid advancement in technology, understanding the functionality of heat simulation software can significantly influence project outcomes. This article aims to equip IT and software professionals, as well as businesses both large and small, with the knowledge necessary to navigate this nuanced landscape. All discussions here will underline the importance of making informed decisions regarding the selection and usage of heat simulation tools.
Brief Description
Overview of the software
Heat simulation software deals with the analysis of thermal phenomena in various materials and systems. Its primary objective is to predict the behavior of a system under different thermal conditions. This can include the design and analysis of electronic components, HVAC systems, automotive parts, and much more. The software incorporates mathematical models and algorithms to simulate heat distribution, conduction, convection, and radiation processes in a user-friendly interface.
Key features and functionalities
- Thermal Analysis: It allows for detailed assessments of thermal profiles in products and materials, which is crucial for ensuring reliability and performance.
- User-Friendly Interface: Most software options prioritize ease of navigation to help engineers and designers visualize thermal dynamics intuitively.
- Integration Capabilities: Many tools are designed to integrate with other CAD or simulation software, facilitating more comprehensive analyses across different domains.
- Reporting Tools: They often include advanced reporting features that help in presenting simulation results comprehensively, assisting in decision-making processes.
System Requirements
Hardware requirements
To run heat simulation software efficiently, certain hardware specifications must be met. These generally include adequate RAM, processing power, and storage capacity. For instance, software such as ANSYS or COMSOL Multiphysics requires a minimum of 8 GB of RAM, although 16 GB or more is recommended for complex simulations. A multi-core processor is also essential for handling simulations without lag.
Software compatibility
Choosing heat simulation software also requires consideration of software compatibility. Most tools are compatible with Windows operating systems; however, it is crucial to verify compatibility based on specific versions. Furthermore, some tools may need additional software libraries or plugins, such as .NET Framework, to operate optimally. Checking the official documentation for each product ensures that the selected software will function effectively within the user’s existing technological ecosystem.
Prologue to Heat Simulation Software
Understanding heat simulation software is crucial for industries that rely on thermal analysis and design. This tool enables professionals to predict how systems will behave under varying thermal conditions. As technology advances, the demand for accurate thermal modeling continues to grow. This section provides insights into what heat simulation is and its significance across different sectors.
Defining Heat Simulation
Heat simulation refers to the use of software to model and analyze thermal processes. It involves the representation of heat transfer phenomena such as conduction, convection, and radiation. These simulations provide valuable insights into thermal performance, enabling engineers and designers to optimize systems before physical prototypes are created.
In the realm of engineering, heat simulation aids in predicting how heat will dissipate or accumulate in various materials and configurations. The accuracy of these simulations is underpinned by complex algorithms and physical models that replicate real-world behavior. The simulation results can inform decisions on material selection, design layouts, and system efficiency.
Importance in Various Sectors
The significance of heat simulation software spans a wide array of sectors:
- Manufacturing: Heat simulation is employed to enhance product design and improve production processes. For example, in metal casting, simulations help in understanding how molds will distribute heat during the cooling process.
- Electronics: In electronics, managing heat is vital for ensuring the reliability and longevity of components. Devices such as microprocessors generate substantial heat, and simulations help in optimizing cooling solutions, thereby enhancing performance.
- Architecture: In building design, simulations contribute to energy efficiency by evaluating how buildings respond to solar radiation and internal heat sources. This helps architects create designs that minimize energy consumption.
In each of these instances, the application of heat simulation software leads to improved design, reduced costs, and enhanced performance. With ongoing advancements, the integration of simulation tools into various industries becomes even more beneficial, highlighting the importance of understanding heat simulation.
Fundamental Concepts of Heat Transfer
Understanding the fundamental concepts of heat transfer is essential in the context of heat simulation software. These concepts form the backbone of thermal analyses conducted in various fields, including engineering, manufacturing, and architecture. Effective heat management is crucial for optimizing designs and processes, thereby enhancing productivity and safety. The interplay of conduction, convection, and radiation cannot be understated, as each mode of heat transfer significantly influences the thermal behavior of materials and systems.
Three Modes of Heat Transfer
Conduction
Conduction involves the transfer of heat through a material without any movement of the material itself. It occurs at the molecular level as heat energy causes faster vibrations of molecules, which in turn transfer thermal energy to adjacent molecules. One key characteristic of conduction is that it is most effective in solids. This makes it a popular choice for applications that require precise control over heat distribution. For instance, in manufacturing, understanding conduction allows for the optimization of processes like welding and casting.
A unique feature of conduction is its dependence on the thermal conductivity of materials. Thermal conductivity is a measure of a material’s ability to conduct heat, and higher conductivity values indicate better heat transfer capabilities. However, when using conduction in heat simulation, one must consider potential disadvantages, such as heat loss to the environment, which can lead to inefficiencies.
Convection
Convection is the transfer of heat due to the movement of fluids, including liquids and gases. It can be classified into natural and forced convection. Natural convection occurs when fluid motion is caused by temperature differences, while forced convection involves external forces like fans or pumps to enhance fluid movement. The key characteristic of convection is its reliance on fluid dynamics, making it especially relevant in applications related to HVAC systems and cooling technologies.
A distinct aspect of convection is its ability to provide rapid heat transfer over a larger area compared to conduction. This feature makes it beneficial in scenarios where swift temperature adjustments are necessary. On the downside, convection can complicate heat simulations because it is influenced by factors such as fluid velocity and turbulence, which can lead to increased complexity in modeling.
Radiation
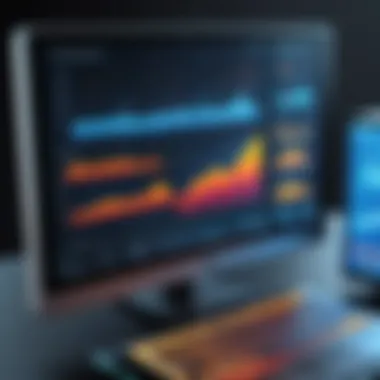
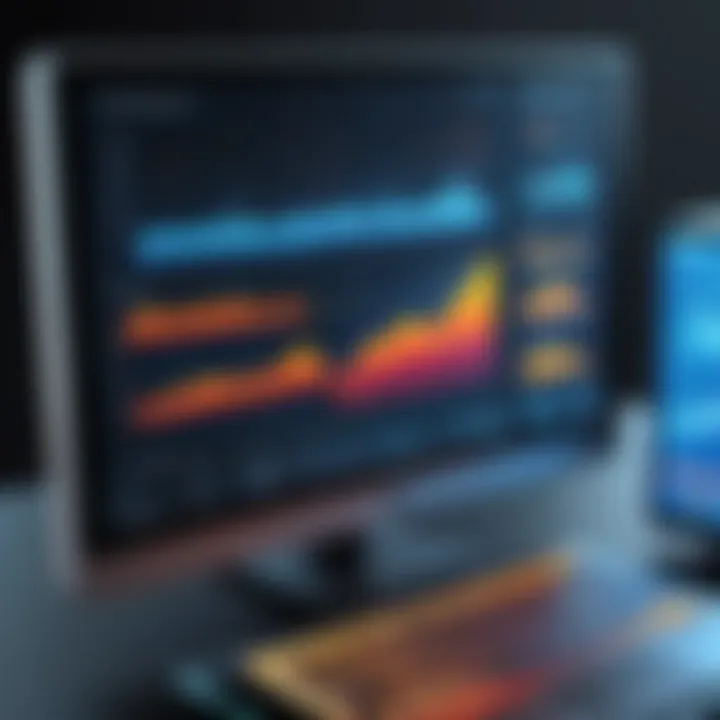
Radiation is the transfer of heat through electromagnetic waves and does not require a medium, which means it can occur in a vacuum. This mode is particularly significant in high-temperature environments, such as furnaces and reactors, where heat transfer needs to occur quickly and efficiently. A key characteristic of radiation is its dependence on the surface temperature and emissivity of materials.
Radiative heat transfer is a beneficial choice for applications exposed to extreme conditions because it is less constrained by material properties compared to conduction and convection. One unique feature of radiation is its ability to be modeled in terms of surface characteristics, which can simplify simulation processes. However, the disadvantages include that it is less effective over greater distances and can add complexity due to the interaction between multiple surfaces.
Thermal Conductivity and Its Role
Thermal conductivity is a critical parameter in heat transfer and plays a significant role in heat simulation software. It defines how well a material can conduct heat and varies widely among different materials. Materials with high thermal conductivity, such as metals, facilitate efficient heat transfer, while insulating materials like foam exhibit low thermal conductivity, effectively reducing heat loss. Understanding the thermal conductivity of materials is essential for accurate simulations, as it influences the heat distribution and overall thermal performance of a system.
Incorporating thermal conductivity values in simulations enables engineers and designers to predict how structures will respond under various thermal conditions. Accurate data leads to better decision-making, whether improving energy efficiency in buildings or ensuring reliability in electronic components.
Key Features of Heat Simulation Software
Heat simulation software serves as an essential tool in various industries where heat management is crucial. Understanding the key features of this software can greatly enhance its utility and effectiveness. As technology advances and the demands for precision in heat-related calculations increase, these features become vital for engineers and professionals.
User Interface and Usability
A user-friendly interface is one of the core pillars of effective heat simulation software. A clear, well-designed interface allows users to navigate through complex data and tools with ease. For IT professionals, having intuitive controls drastically reduces the time needed to learn the system. Developers often include customizable dashboards, which enable users to prioritize relevant data. This customization enhances productivity, allowing engineers to focus on problem-solving rather than struggling with the software.
Efficient usability also extends to support documentation and tutorials. A range of learning resources fosters a deeper understanding of the software’s capabilities, promoting confidence in its application. Therefore, prioritizing user experience leads to enhanced engagement and results. In a competitive environment, effective user interfaces stand out.
Data Visualization Capabilities
Data visualization is another critical feature within heat simulation software. The ability to generate clear and comprehensible visual representations of complex data sets is essential. Visualization tools can include graphs, charts, and 3D models that help clarify the dynamic processes of heat transfer.
With features like heat maps, users can quickly identify areas of high and low thermal activity. This visual insight aids in decision-making processes, allowing users to adjust design parameters efficiently. Furthermore, the ability to animate simulation results offers an interactive approach, making it simpler to communicate findings to stakeholders or team members. In summary, robust data visualization enhances the software's utility and increases understanding among users.
Integration with Other Tools
Integration capabilities are increasingly becoming a necessity in heat simulation software. Many projects require collaboration between various software tools. For instance, being able to connect with CAD software like AutoCAD or SolidWorks allows for seamless data transfer. This integration avoids redundant data entry and errors while ensuring consistency across platforms.
Furthermore, compatibility with databases and analytical tools enhances the power of simulations. For instance, some software can link with MATLAB to conduct further mathematical or statistical analysis, thereby providing more comprehensive insights into thermal behavior. This collaborative capability makes heat simulation software not just a standalone solution but part of a larger ecosystem of engineering tools.
Applications of Heat Simulation Software
Heat simulation software plays a vital role in various sectors, enabling professionals to visualize and analyze thermal behavior in a controlled environment. Understanding these applications can significantly improve product design and efficiency. This section delves into three primary fields where heat simulation software has proven beneficial: manufacturing and materials science, electronics and electrical engineering, and architecture and building design.
Manufacturing and Materials Science
In the manufacturing sector, heat simulation software aids in optimizing process design, reducing production costs, and enhancing product performance. By forecasting heat distribution and transfer in materials, engineers can identify critical areas that may suffer from thermal stress or failure. For example, when designing metal parts, it's crucial to understand how different alloys react to heat during processes like welding or casting. Thus, using heat simulation tools can lead to stronger and more reliable end products.
Additionally, materials scientists utilize these simulations to analyze thermal conductivity and phase changes. Insights from simulations not only inform material selection but also assist in creating new materials with desired thermal properties. The ability to virtually test materials saves time and resources, allowing for a more efficient R&D process.
Electronics and Electrical Engineering
The electronics industry relies heavily on heat simulation software to design components that must operate within strict thermal limits. Devices like CPUs, GPUs, and power electronics generate considerable heat, which must be effectively managed to ensure reliability. Heat simulation allows engineers to model thermal performance under various operating conditions, leading to designs that maintain optimal operating temperatures.
Moreover, the software can help evaluate cooling systems, such as heat sinks and fans, to ensure they can handle the expected thermal load. For instance, thermal simulations can predict how air flows over a circuit board, guiding engineers to make adjustments that enhance cooling efficiency. In doing so, the overall lifespan and performance of electronic devices improve.
Architecture and Building Design
In architecture, heat simulation software plays a critical role in sustainable design. Architects can simulate how buildings respond to environmental heat gain and loss, achieving higher energy efficiency. By analyzing sunlight exposure, building orientation, and thermal mass, it's possible to design structures that minimize heating and cooling costs.
Furthermore, software tools help identify hot and cold spots within a building, guiding the placement of heating and cooling systems. The ability to visualize temperature distributions enables better decision-making during the design phase, ultimately enhancing occupant comfort and reducing energy use.
"The integration of heat simulation software in architecture can lead to significant advancements in energy efficiency and comfort for occupants."
Advantages of Utilizing Heat Simulation Software
Using heat simulation software offers significant advantages across various sectors. Understanding these benefits is crucial for businesses and individuals seeking effective solutions for thermal management and analysis. The efficiencies presented by these tools can translate into direct cost savings and enhanced project outcomes. Below, we detail two major advantages: cost efficiency and enhanced accuracy.
Cost Efficiency
One of the primary benefits of heat simulation software is its potential for cost savings. Traditional methods of analyzing heat transfer often involve extensive empirical testing, which can be expensive and time-consuming. Utilizing simulation software allows for virtual testing and modeling, significantly reducing the need for physical prototypes and experiments.
- Reduced Material Waste: By simulating different scenarios, engineers can identify optimal designs and materials before production. This minimizes trial and error, saving both time and resources.
- Shortened Development Cycle: Simulation accelerates the design process. The ability to run multiple simulations in a short time frame enables faster decision-making. Businesses can bring products to market quicker, gaining a competitive advantage.
- Lower Energy Costs: Accurate thermal analysis can lead to better designs that use less energy in operation. Efficient systems often have lower long-term energy requirements, creating savings that extend beyond initial development.
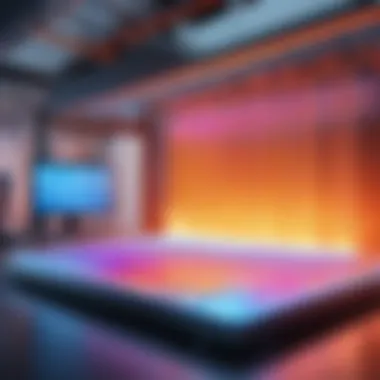
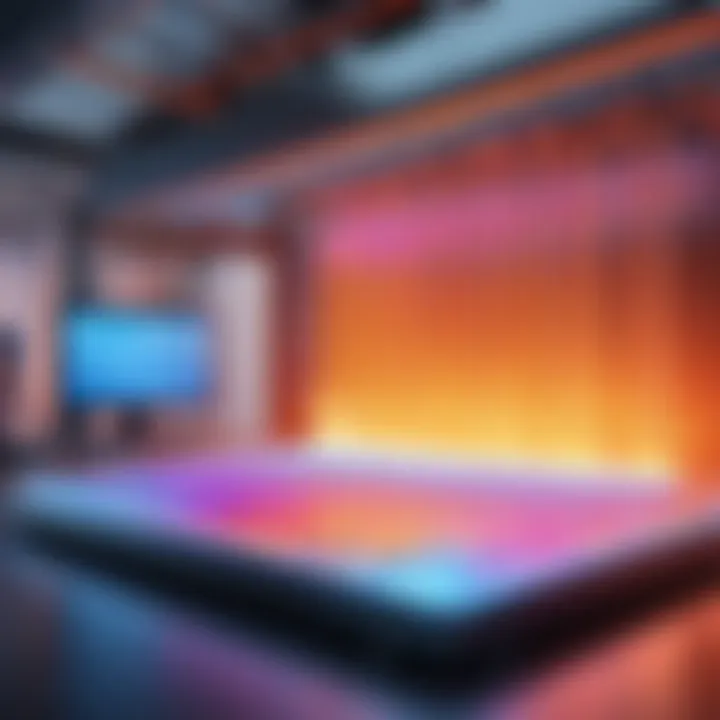
Overall, heat simulation software not only curtails expenses related to development and testing but also contributes to reduced operational costs.
Enhanced Accuracy
Accuracy is vital in the design and implementation of thermal systems. Heat simulation software excels at providing precise data for various conditions and applications. This level of clarity leads to informed decision-making.
- Complex Calculations: Modern simulation tools handle complex mathematical models that consider various factors affecting heat transfer. This capability ensures reliable predictions about performance and behavior under different scenarios.
- Improved Design Validation: With simulation, designers can validate their concepts against real-world conditions, which reduces risks associated with design flaws. The software can reveal potential issues before physical implementation, safeguarding investments.
- Data-Driven Insights: Engineers gain detailed insights from simulation results, enabling them to make evidence-based adjustments during the design phase. This results in designs that meet specifications with greater precision.
The integration of accurate data into the decision-making process fundamentally changes how industries approach thermal management.
Challenges in Heat Simulation Software Implementation
The implementation of heat simulation software brings numerous benefits, but it is not without its challenges. Understanding these obstacles is crucial for users and decision-makers alike. The challenges can significantly affect both the effectiveness of heat analysis and the overall success of projects that depend on this technology. Addressing these issues can optimize the utilization of heat simulation tools and foster better decision-making processes in various industries.
Data Quality and Availability
One major challenge is the quality and availability of data. For any simulation software to provide accurate results, it needs high-quality input data. This includes material properties, environmental conditions, and operational parameters. If the data is incomplete, outdated, or inaccurate, the simulation results will reflect these deficiencies, leading to suboptimal design choices and potential failures.
Businesses often face difficulties in acquiring reliable data due to various factors, including the lack of standardized testing methods across different materials or the absence of comprehensive databases. Furthermore, if data is sourced from multiple suppliers, discrepancies may arise, complicating the validation process.
To mitigate these issues, organizations should invest in robust data management systems. This can include standardized protocols for data collection, validation methods to ensure the accuracy of provided information, and accessible databases providing reliable materials data. By addressing the data quality challenge, firms can attain stronger modelling capabilities and more reliable simulation outcomes.
Software Complexity and Learning Curve
Another significant hurdle in implementing heat simulation software is its complexity and the associated learning curve. Advanced simulation tools often include a wide array of features and functionalities which can be daunting for new users. The sophisticated nature of these programs demands a certain level of expertise that not all users possess initially.
Training staff to effectively utilize these tools can require significant time and financial resources. This aspect becomes especially challenging in small businesses where budgets and personnel are limited. As a result, organizations might underutilize the software capabilities or even abandon the software altogether in favor of simpler, less effective alternatives.
To facilitate smoother integration, companies should consider developing tailored training programs for their staff. Investing in user-friendly software with extensive help resources and community support can also ease the transition. Moreover, an incremental approach to software deployment—starting with basic features and gradually introducing more complex aspects—can help users adapt to the software more easily. By doing so, companies can overcome the learning curve and maximize the potential of their heat simulation tools.
Evaluating Heat Simulation Software
Evaluating heat simulation software is critical for both individual users and organizations seeking to optimize their thermal management solutions. Given the complexity and variety of software available, a thorough evaluation process is needed to ensure the selected tool meets specific project requirements. This section will focus on essential aspects such as the criteria for selecting software and a comparative analysis of popular tools in the market.
Criteria for Selection
When tasked with selecting heat simulation software, several factors play a pivotal role in the decision-making process. The following criteria should be considered:
- Feature Set: The software should offer a wide array of capabilities, including various simulation techniques such as conduction, convection, and radiation. Look for tools with advanced features like real-time analysis and multi-physics modeling.
- Usability: The learning curve can greatly affect productivity. A user-friendly interface enhances the speed at which team members can become proficient. Evaluate whether the software provides adequate documentation and customer support.
- Integration: Assess how well the software integrates with other tools and platforms used within the organization. Compatibility can save time and reduce errors in data transfer.
- Cost: Analyze the overall cost of ownership, including licensing fees, training, and support services. A high initial cost may be justified by long-term operational savings and efficiencies gained.
- Performance Metrics: Look for benchmarks or case studies that demonstrate the software's effectiveness in real-world applications. Performance metrics can reveal insights into the reliability and accuracy of simulations.
Comparative Analysis of Popular Tools
A robust understanding of the strengths and weaknesses of leading heat simulation software can empower users to make informed decisions. Here are some notable options:
- ANSYS Fluent: Known for its powerful computational fluid dynamics (CFD) capabilities, ANSYS Fluent excels in simulating heat transfer in complex geometries. Its extensive features are ideal for industries where precision and efficiency are critical.
- COMSOL Multiphysics: This software offers an integrated environment for modeling various physical phenomena, including heat transfer. Its flexibility in coupling different physics makes it a preferred choice for researchers and engineers.
- SolidWorks Flow Simulation: Particularly useful for engineers familiar with SolidWorks CAD software, this tool allows for seamless integration and intuitive simulations of thermal conditions within designs.
- ** Autodesk CFD**: Providing advanced thermal analysis features, Autodesk CFD is often favored in design environments. Its capabilities in real-time visualization can assist in quickly assessing design performance.
"Selecting the right heat simulation software is a decisive factor in achieving project success. The integration of the tool into the workflow can boost efficiency and accuracy significantly."
In summary, evaluating heat simulation software involves a multifaceted approach. Understanding the specific needs of the user and the industry helps to narrow down the options effectively. By focusing on criteria such as features, ease of use, integration, cost, and performance, it's possible to make a well-informed choice in selecting the right software.
For more detailed information on specific software tools, you can visit Wikipedia, Britannica, Reddit, or Facebook.
Future Trends in Heat Simulation Software
The landscape of heat simulation software is evolving rapidly, driven by advancements in technology and the increasing demand for accurate simulations across various sectors. Understanding future trends in this domain is essential, not just for software developers but also for IT professionals and businesses aiming to enhance their operational efficiencies. The importance of staying updated with these trends lies in the ability to leverage cutting-edge solutions, which can ultimately result in better design processes, reduced costs, and increased competitiveness in the market.
Integration of AI and Machine Learning
The integration of Artificial Intelligence (AI) and Machine Learning (ML) is reshaping heat simulation software significantly. These technologies offer advanced algorithms that can predict temperature distributions and heat flow with a level of accuracy that traditional methods struggle to achieve. By analyzing large datasets, AI can identify patterns and optimize simulations, leading to more efficient designs.
Moreover, AI-powered simulations can reduce the time required to conduct analyses. This is particularly beneficial in industries such as manufacturing and aerospace, where timely decision-making is crucial. For example, using ML algorithms can help in tuning simulation parameters automatically, allowing for a dynamic response to input changes.
However, a few considerations come with this trend. Companies must ensure they have the proper data infrastructure to support AI and ML implementations. Investing in training for their teams to understand and utilize these technologies effectively is also necessary.
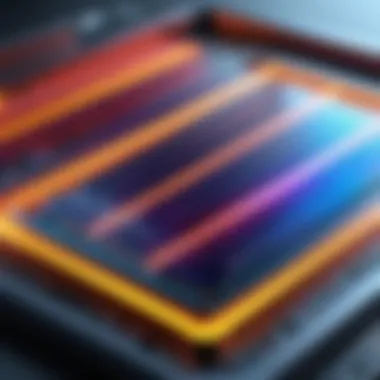
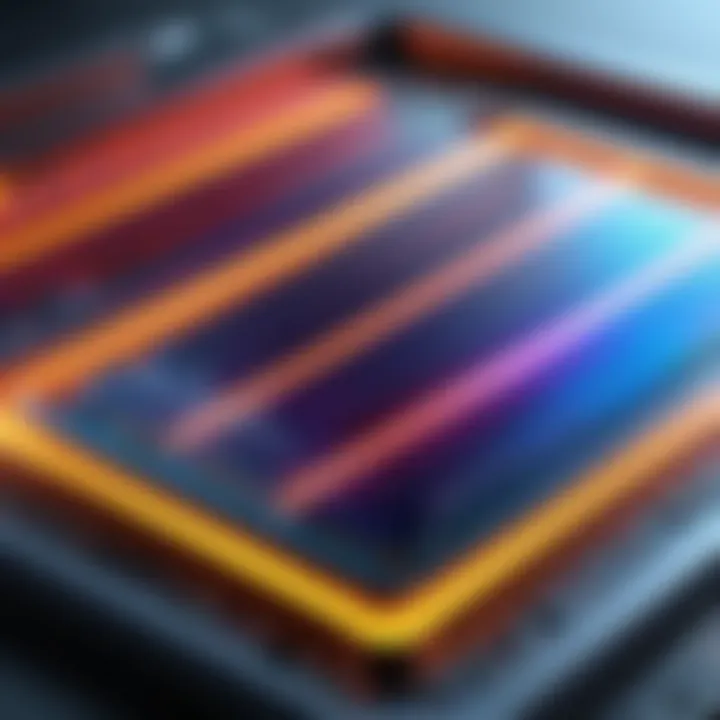
Cloud-Based Solutions
Cloud-based solutions are another significant trend in heat simulation software. The shift to the cloud offers various benefits, such as increased accessibility, scalability, and cost-effectiveness. Users can run simulations on cloud servers without the need for high-end local hardware, which lowers the initial investment barrier for small and large businesses alike.
Cloud solutions also allow for real-time collaboration among teams spread across different locations. This can enhance workflow and provide instant feedback on simulation results. Furthermore, updates and maintenance become easier as they are handled on the cloud provider's end rather than on-site.
Nevertheless, concerns regarding data security and privacy persist. Companies must diligently select cloud providers with robust security measures to protect sensitive information. Additionally, understanding the implications of cloud usage on regulatory compliance is crucial.
"The future of heat simulation software lies at the intersection of technology and innovation, with AI and cloud computing driving the next wave of efficiency and accuracy."
Overall, evaluating these future trends enables businesses to position themselves strategically. Embracing these advancements can lead to improved simulation outcomes and more informed decision-making.
Case Studies and Practical Applications
Case studies and practical applications of heat simulation software serve as a bridge between theoretical knowledge and real-world implementation. This section emphasizes the vital role that these applications play in showcasing how heat simulation tools can be effectively used across various industries. By analyzing real-world scenarios, professionals can glean insights into best practices, challenges encountered, and innovative solutions that have emerged from using these tools.
Industrial Use Cases
In the industrial sector, heat simulation software finds numerous applications, significantly improving efficiency and performance. One prominent example is in the automotive industry, where engineers use software like ANSYS Fluent to simulate heat distribution during the design phase of engines and exhaust systems. This capability allows for the identification of potential overheating issues before physical prototypes are built, saving both time and resources.
Another area is in semiconductor manufacturing. Companies such as Intel utilize COMSOL Multiphysics to model heat transfer in microprocessors. By simulating thermal properties, these firms can optimize their designs for better performance, leading to enhanced energy efficiency and longer product lifespans.
Furthermore, in the oil and gas industry, software tools like Aspen HYSYS are employed to analyze heat transfer in drilling operations. This application helps improve safety by modeling temperature profiles in real-time, ensuring that operators can make informed decisions based on accurate data regarding risks and operational efficiency.
Research and Development Insights
The realm of research and development benefits significantly from heat simulation software. In academic and corporate research environments, tools such as SolidWorks Flow Simulation and Autodesk CFD provide researchers the ability to perform detailed thermal analyses on innovative materials and technologies. For instance, scientists exploring advanced composite materials can use these simulations to predict thermal performance under various conditions, thus offering insights that guide further experimentation.
Moreover, research institutions often collaborate with software providers for customized simulations tailored to their unique needs. This partnership can lead to groundbreaking discoveries in fields like renewable energy, where heat simulation plays a critical role in the design of solar panels and other thermal energy systems. By simulating various environmental conditions and materials, researchers can enhance energy capture and efficiency.
"Real-world applications of heat simulation software not only validate its utility but propel innovation across diverse sectors."
Best Practices for Effective Simulation
Effective simulation in heat simulation software is key for achieving accurate and reliable results. The practices outlined below ensure that users can make the most of their simulation efforts, leading to informed decision-making and better outcomes in various applications.
Validation of Simulation Results
Validation is a crucial step in the simulation process. It confirms that the heat simulation software produces results consistent with real-world outcomes. Without proper validation, the integrity of the simulation results can be questionable. Here are some important elements to consider during this process:
- Benchmarking: Compare simulation results against established benchmarks or experimental data. Any discrepancies should be analyzed to understand their causes.
- Sensitivity Analysis: This helps in identifying how sensitive the simulation outputs are to different input parameters. It can assist in pinpointing critical variables that could influence the results.
- Documentation: Maintain thorough records of each simulation scenario, including assumptions, input parameters, and validation protocols. This documentation can aid future projects and ensure reproducibility of results.
The benefits of validation include increased confidence in results and the ability to make data-driven decisions. It becomes essential in industries ranging from manufacturing to aerospace, where even minor deviations can lead to significant consequences.
Iterative Simulation Approaches
Iterative simulation refers to running multiple simulations, refining parameters in each cycle based on previous outputs. This approach allows for continuous improvement in the accuracy of the simulation results. Key considerations include:
- Refinement of Inputs: After each simulation run, review input parameters. Adjust them to reflect findings from the last iteration, thus enhancing the accuracy of future results.
- Feedback Loops: Integrate feedback from stakeholders in the simulation process. Their insights can lead to better parameter adjustments and more relevant simulations.
- Resource Management: Ensure appropriate allocation of computing resources. Iterative methodologies may require significant processing power, so optimizing resource use is essential.
Using iterative approaches provides several advantages, such as discovering optimal conditions for designs or processes and improving the overall reliability of simulation outcomes. This method empowers users to build upon their previous work, ultimately resulting in a deeper understanding of thermal behavior.
"In simulation, each run is a step towards greater accuracy and reliability. Embrace the process for improved insights."
Closure
The conclusion of this article serves as a critical juncture in understanding the comprehensive landscape surrounding heat simulation software. This segment not only encapsulates the key takeaways but also prepares the audience for future considerations in the field. It is essential to reflect on the profound impact such software has across various sectors. From manufacturing to architecture, its utility extends beyond mere calculations to influencing major design and operational decisions.
Summarizing Key Insights
Heat simulation software allows professionals to predict temperature distributions and heat flows in different materials and environments. Throughout this article, we have detailed various aspects of its usage, engineering principles, and best practices. Key insights include:
- Understanding the modes of heat transfer can enhance the effectiveness of simulations.
- The importance of user-friendly interfaces cannot be overstated; they facilitate broader adoption across industries.
- Validating simulation results is crucial to ensuring accuracy and reliability.
By recognizing these elements, one can appreciate the depth of knowledge necessary to utilize heat simulation tools effectively. The advantages greatly outbalance the challenges when implemented correctly, thus positioning organizations to innovate and improve productivity.
The Path Forward
As industries continue to evolve, the direction of heat simulation software is poised for transformation. With advancements in artificial intelligence and machine learning, the integration of smart algorithms can create models that operate in real-time, adapting to variable conditions.
Moreover, the rise of cloud-based solutions enhances accessibility, allowing teams to collaborate and share findings seamlessly across geographic boundaries.
To maintain competitiveness, decision-makers in IT and software development must prioritize these trends. Adapting to a landscape that is increasingly informed by data and automation will be crucial. The future of heat simulation software promises to be vibrant and dynamic, offering new solutions that respond to unique user needs.