Harnessing PIM for Effective Inventory Management

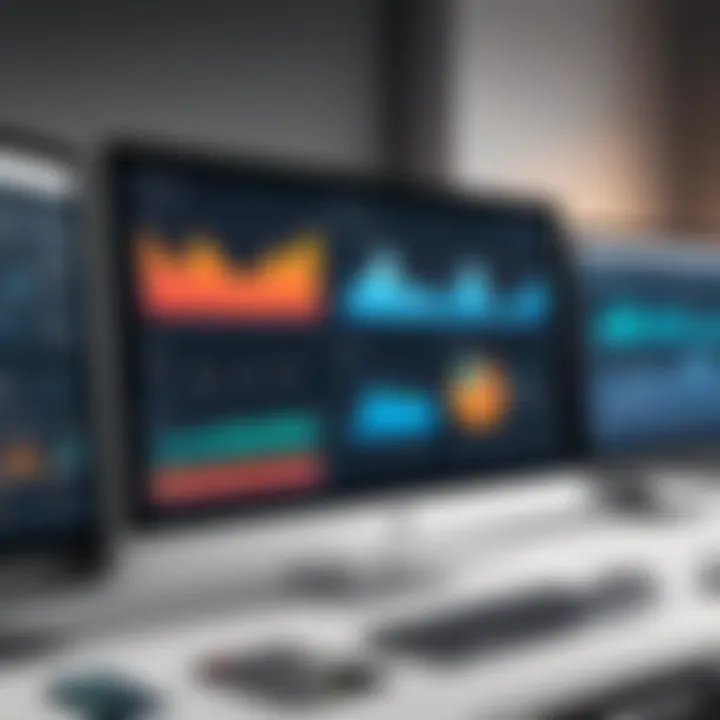
Intro
In today's fast-paced commercial environment, effective inventory management is crucial for any business that aims for efficiency and growth. One of the key components contributing to this is Product Information Management (PIM). PIM is a system that manages all information related to a company's product portfolio. It provides a centralized place for product data, enabling businesses to maintain accurate and consistent information across all platforms.
This article will explore various facets of PIM and its indispensable role in inventory management. Businesses of all sizes can benefit significantly from utilizing PIM systems, as they streamline processes, enhance accuracy, and ultimately drive productivity.
Brief Description
Overview of the software
PIM software serves as the backbone of product data management. This tool allows businesses to gather, store, and distribute product information effectively. PIM systems can handle a vast array of data types, including descriptions, specifications, images, and even marketing assets. The dynamic nature of today's commerce demands that product data be readily accessible and consistently updated, which is where PIM excels.
Key features and functionalities
Some of the notable features of PIM systems include:
- Centralized Database: All product information is stored in one location, making updates easier and more efficient.
- Data Quality Control: Ensures high data quality with validation rules and error checks.
- Integration Capabilities: PIM systems can seamlessly integrate with e-commerce platforms, ERP systems, and other software.
- Multi-channel Management: Oversees product data across various sales channels, including online, retail, and marketplaces.
- Customizable Workflows: Companies can adapt workflows to their specific needs for data approval and publishing.
System Requirements
Hardware requirements
When implementing PIM, hardware specifications depend on the selected software solution. However, a robust server that can handle large data sets and multiple concurrent users is usually necessary. Adequate storage and memory are vital for ensuring smooth operation.
Software compatibility
Compatibility with current systems is critical when selecting a PIM solution. Most PIM solutions work with various platforms, such as Magento, Shopify, and Salesforce. A thorough review of the PIM's integration options ensures that it aligns with existing software infrastructures.
Understanding PIM and Its Relevance
Product Information Management (PIM) has emerged as a critical element in modern inventory management. Understanding PIM is essential for both small and large businesses since it directly relates to how they handle product data, enhance inventory efficiency, and optimize customer experience. Several specific elements underscore the importance of understanding PIM in this context.
First, as products become increasingly diverse and complex, managing product information effectively is vital. PIM centralizes product data, which ensures that all stakeholders have access to consistent and accurate information. This is particularly beneficial in sectors where product listings change frequently, such as retail and e-commerce.
Second, accurate product data can significantly impact business decisions. Incorrect or outdated information can lead to inventory mismatches, redundant stock, or even loss of sales. For instance, an e-commerce site that displays wrong pricing or product specifications may confuse customers, resulting in abandoned carts. A robust PIM system mitigates these risks by maintaining data accuracy across all channels.
Third, PIM serves as a strategic asset. It not only streamlines product information but also enhances collaboration across teams. Marketing, sales, and inventory management can all access the same data, ensuring that everyone is on the same page. This interconnectedness fosters better decision-making and enhances response times in a fast-paced market.
To sum it up, an understanding of PIM and its relevance is not just beneficial, but necessary for businesses aiming to thrive in competitive environments. By fostering precise data management, enhancing collaboration, and supporting operational efficiencies, PIM acts as a backbone for effective inventory management.
Definition of PIM
Product Information Management (PIM) refers to the processes and systems used to manage product data throughout its lifecycle. This includes collecting, enriching, and distributing product information to various channels. PIM systems are designed to centralize product information in a single repository, allowing organizations to maintain data consistency and accuracy.
For example, a PIM system can store details about product specifications, images, pricing, and descriptions. This centralized data is crucial for organizations that operate on multiple sales channels, including websites, mobile apps, and physical stores.
Importance of Data Accuracy
In today's business landscape, the accuracy of data cannot be overstated. For effective inventory management, businesses must ensure that product information reflects reality. Data accuracy impacts inventory levels, order fulfillment, and customer satisfaction.
Without a reliable PIM system to manage this data, a company may suffer from:
- Stock discrepancies: This can lead to either excess inventory or stockouts.
- Customer complaints: Inaccuracies can frustrate customers, driving them to competitors.
- Operational inefficiencies: Poor data can result in wasted time and resources when managing products.
Therefore, maintaining a high standard of data accuracy through PIM is crucial for minimizing risks and bolstering operational performance.
PIM as a Strategic Asset
Viewing PIM as a strategic asset allows organizations to leverage product data for various competitive advantages. When implemented correctly, a PIM system can support an organization's strategic initiatives by:
- Driving marketing efforts: Accurate and rich product information enhances marketing campaigns, leading to higher conversion rates.
- Improving customer experiences: Quick access to comprehensive product information heightens customer satisfaction and loyalty.
- Facilitating compliance: As regulations evolve, PIM helps comply with industry standards and legal requirements regarding product information.
Thus, PIM is not merely a tool for inventory management but a crucial component of a company’s larger strategic framework.
The Intersection of PIM and Inventory Management
Product Information Management (PIM) and inventory management share a critical relationship that enhances overall effectiveness in business operations. This section aims to elaborate on how PIM can support inventory management, providing clarity on product data and facilitating informed decision-making.
Streamlining Product Data
A key advantage of PIM in the context of inventory management is its ability to streamline product data. PIM centralizes data from different sources, ensuring that all product information—be it specifications, images, or descriptions—is consistent and accurate. This uniformity reduces discrepancies that can lead to inventory mishaps. For instance, when all stakeholders access the same updated information, they can effectively track inventory levels, manage stock movements, and respond to demand fluctuations with confidence. Streamlined data also supports better forecasting methods, enabling businesses to anticipate stock needs and optimize their supply levels.
Enhancing Inventory Visibility
Enhancing inventory visibility is another significant benefit achieved through the integration of PIM with inventory management systems. With comprehensive access to product information, stakeholders can obtain real-time insights into inventory levels across multiple locations. This real-time visibility helps in identifying slow-moving items, as well as in recognizing trends that may require strategic adjustments. When employees can see what is available at a glance, they make quicker, more informed decisions, which can lead to reduced holding costs and improved customer service.
Integration with Supply Chain Processes
The effective integration of PIM with supply chain processes facilitates seamless operations throughout the inventory management system. This synchronization ensures that both product data and inventory levels are aligned, enabling efficient stock replenishment and accurate order fulfillment. A well-integrated system reduces lead times and minimizes the risk of stockouts or overstocking. Companies can manage their products with agility and respond effectively to changing market demands. Furthermore, by establishing strong ties between PIM and supply chain operations, businesses gain a competitive edge and drive overall efficiency.
Importantly, the intersection of PIM and inventory management not only enhances the efficiency of operations but also reinforces customer satisfaction through improved product availability and delivery precision.
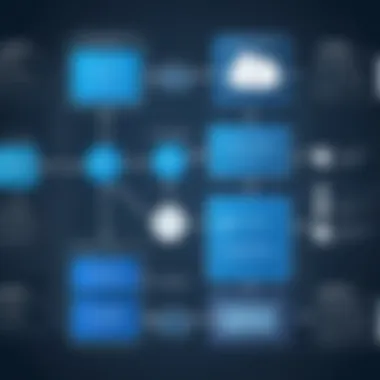
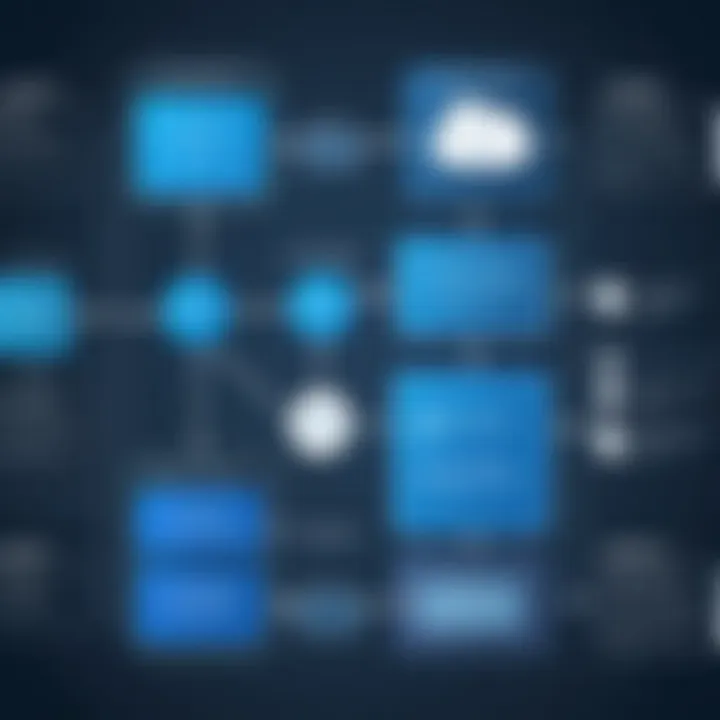
In summary, PIM serves as a vital tool in inventory management. It streamlines product data, enhances visibility, and integrates with supply chain processes, encouraging effective decision-making and operational efficiency.
Key Features of Effective PIM Systems
Product Information Management (PIM) systems are essential in today's data-driven marketplace. Their design focuses on managing product data efficiently, facilitating improved inventory management. These systems consolidate and streamline critical product information, making it accessible and actionable. Understanding key features of effective PIM systems can significantly impact how businesses operate.
Centralized Data Management
Centralized data management serves as the backbone of any effective PIM system. By consolidating product information into a single source, organizations eliminate redundancies and errors. A well-organized PIM database allows teams to access real-time data easily. This visibility is crucial for maintaining accurate inventory levels.
The benefits of centralized data management include:
- Reduction of Data Silos: Information across departments becomes cohesive. This alignment leads to more informed decision-making.
- Improved Collaboration: With all product information in one place, teams can work together seamlessly.
- Time Efficiency: Teams spend less time searching for data and more on leveraging it.
Automation Capabilities
Automation is another prominent feature of successful PIM systems. Automated processes reduce manual input, leading to fewer errors. By automating tasks such as data entry and updates, businesses can ensure that their product information is always current.
Key advantages of automation in PIM include:
- Speed: Faster data processing saves time across the entire inventory management process.
- Consistency: Automated workflows enforce standards, ensuring uniformity in product information.
- Cost Effectiveness: Reducing manual labor can lead to lower operating costs, improving overall efficiency.
Multichannel Distribution Support
In the modern marketplace, businesses often operate across multiple sales channels. Effective PIM systems provide support for multichannel distribution, allowing companies to manage their product data across various platforms. This capability aids in presenting consistent product information to customers regardless of the channel they choose.
Essential benefits of multichannel distribution support include:
- Streamlined Management: PIM systems enable easier updates across numerous channels, maintaining consistency.
- Enhanced Customer Experience: Customers access accurate product information whether shopping online or in store.
- Market Expansion: With effective PIM, businesses can easily explore new channels and reach broader audiences.
"Investing in effective PIM systems can drive substantial operational improvements and boost customer satisfaction."
In summary, key features like centralized data management, automation capabilities, and multichannel distribution support create a robust PIM system. Understanding these elements helps businesses capitalize on the full potential of their product information management efforts.
Choosing the Right PIM Solution
Selecting an appropriate Product Information Management (PIM) solution is critical for organizations looking to maximize their inventory efficiencies. The right PIM software ensures accurate product data, streamlined processes, and improved customer satisfaction. Here, we focus on three key areas in making an informed choice: assessing business needs, evaluating software options, and considering scalability.
Assessing Business Needs
Understanding the specific needs of your business is the first step in choosing a PIM solution. Each organization has unique requirements based on factors like industry, size, and operational complexity. Start by conducting a thorough analysis of your current product data management processes. Here are some considerations:
- Internal Challenges: Identify pain points in your existing systems, such as data inaccuracies or inefficient workflows.
- Business Goals: Define what you want to achieve with PIM. Common goals include increasing data accuracy and enhancing product visibility.
- User Requirements: Involve stakeholders from various departments to gather insights. Their experiences will inform the necessary features and functionalities for the system.
Evaluating Software Options
Once you have clarified your needs, it’s time to explore software options. The market offers a variety of PIM systems, each with distinct capabilities. Here are key aspects to evaluate:
- Integration Capabilities: Ensure the PIM solution can seamlessly integrate with your existing systems like ERP and CRM.
- User Interface: The usability of the software is crucial. A system that is intuitive will require less training and lower resistance from employees.
- Functionality: Look for features that support your specific needs, such as bulk data import/export, multi-channel syndication, and custom reporting.
Consideration of Scalability
Scalability is another vital aspect when choosing a PIM solution. As your business grows, your product data needs may evolve. A PIM system should adapt to changing demands without significant additional investments in technology.
- Future-Proof Design: Opt for a solution that offers flexibility in adding new features or modules as needed.
- Performance Metrics: Evaluate how the system performs under increased load or during peak seasons.
- Vendor Support: Choose a vendor known for their customer support and commitment to product enhancements over time.
Best Practices for PIM Implementation
In the evolving landscape of inventory management, ensuring the effective implementation of Product Information Management (PIM) systems is crucial for optimizing operations. Effective PIM implementation not only improves data quality but also enhances overall efficiency and agility in managing product information. By following best practices in this domain, organizations can gain substantial competitive advantage while mitigating common pitfalls. Therefore, understanding and applying these practices is vital for businesses aiming to fully leverage the potential of PIM.
Data Quality Management
Maintaining high data quality is central to successful PIM implementation. This involves ensuring that product information is accurate, complete, and up-to-date. High-quality data reduces error rates in inventory management, leading to a more reliable supply chain.
Organizations should establish clear guidelines and protocols for data entry and updates. Regularly reviewing and cleansing data can help eliminate inaccuracies. Using tools that automatically validate product data against predefined schemas can also enhance quality controls.
Key considerations include:
- Establishing data governance policies.
- Implementing checks for data consistency.
- Leveraging automation for data updates.
"Data quality is not just a technical issue; it's a business strategy."
By prioritizing data quality management, companies can ensure that their PIM systems provide accurate insight for decision-making, ultimately driving better inventory performance.
Employee Training and Engagement
One of the most overlooked aspects of PIM implementation is the human factor. Engaging employees and providing thorough training is crucial for maximizing the effectiveness of PIM systems. Employees who understand the importance of PIM and their roles within the framework tend to utilize the systems more effectively.
Training should be tailored to different user roles, ensuring that all employees can leverage the PIM system according to their specific responsibilities. Regular workshops and feedback sessions can enhance user comfort and proficiency with the software.
Key elements of effective training include:
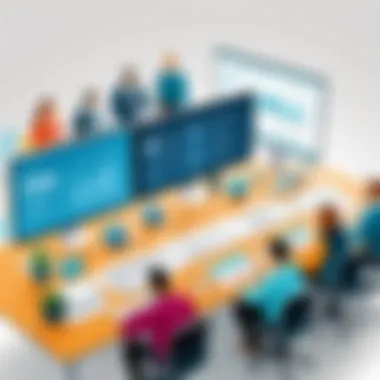
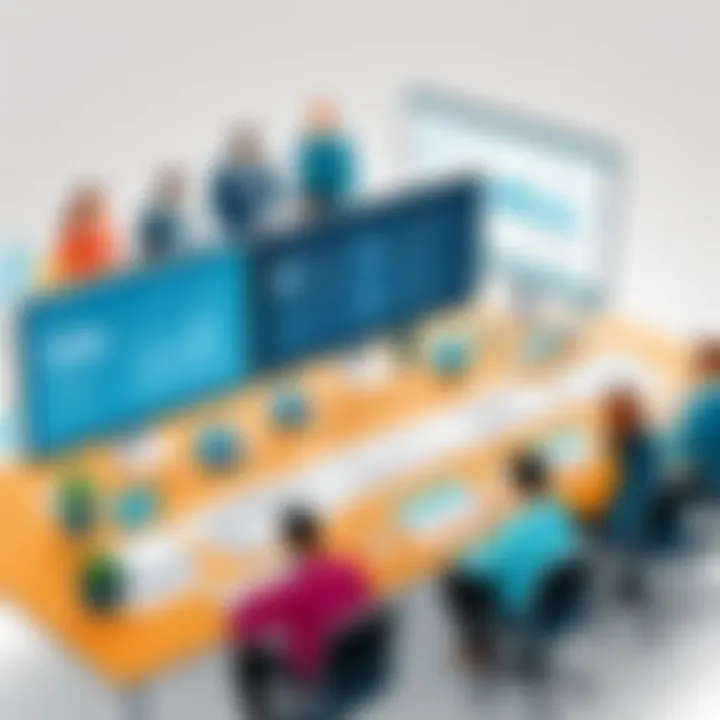
- User-centric training sessions.
- Providing resources and documentation.
- Encouraging continuous learning and adaptation.
A well-trained team can significantly reduce mistakes and enhance productivity, leading to costly errors being avoided during inventory management processes.
Regular System Audits
Conducting regular audits of the PIM system is crucial for identifying potential issues before they escalate. System audits help ensure that the data remains accurate, and the software functions as intended. It is an ongoing process that can help keep both the software and workflow streamlined.
Audits should cover data consistency, compliance with governance policies, and system performance metrics. This practice fosters accountability and encourages continuous improvement.
Benefits of implementing regular audits include:
- Early identification of data inconsistencies.
- Enhanced compliance with data policies.
- Continuous optimization of system performance.
By adopting a proactive approach to system audits, organizations can maintain the integrity and reliability of their product information, which is essential for seamless inventory management.
Challenges in PIM and Inventory Management
The implementation of Product Information Management (PIM) systems is not without its challenges. Recognizing these challenges is crucial for businesses aiming to leverage PIM for enhanced inventory management. Effective inventory management relies heavily on accurate and accessible product information. Therefore, an understanding of these challenges can inform better strategies and solutions.
Data Silos
Data silos represent a significant obstacle in PIM and inventory management. They occur when different departments or systems within an organization store data independently and do not share it with each other. This isolation can lead to inconsistent information, multiplying errors across the operations.
For instance, if the marketing department uses one dataset that does not sync with the inventory data, product details may differ significantly. Such discrepancies can affect product availability, resulting in customer dissatisfaction and potentially lost sales. Overcoming data silos requires a strategic approach aimed at fostering collaboration across departments and facilitating integrated data systems that allow seamless information flow.
Resistance to Change
Another considerable barrier in adopting PIM solutions lies in resistance to change. Organizations often face pushback from employees who are accustomed to long-standing processes. This resistance can stem from a fear of new technology or skepticism regarding its effectiveness.
To effectively address this issue, it is essential to prioritize communication. Engaging team members from the beginning and highlighting the benefits of PIM can cultivate a positive mindset toward change. Training programs can also help ease the transition by ensuring that all staff are comfortable with the new tools and processes.
Technology Integration Issues
Integrating new PIM systems with existing technology platforms poses another challenge. Many businesses operate with legacy systems that may not be compatible with modern PIM solutions. This lack of integration can lead to inefficiencies and increased operational costs.
To mitigate integration issues, organizations need to assess their current technology landscape carefully. Selection of the right PIM system should consider compatibility with existing infrastructure. In some cases, employing middleware or APIs may be necessary to bridge the gap between various systems.
Successful integration of PIM systems ultimately relies on thorough planning, collaboration with IT departments, and commitment to a scalable solution that adapts as business needs evolve.
The Future of PIM in Inventory Management
The evolution of Product Information Management (PIM) continues to reshape the landscape of inventory management. As organizations recognize the value of streamlined product data, the role of PIM becomes increasingly critical. This section delves into vital aspects of the future of PIM, focusing on the innovations that drive efficiency, adaptability, and overall success in inventory management.
Emerging Technologies
The landscape of technology is ever-changing, and PIM is no exception. New technologies are reshaping how businesses manage product information and inventory. Cloud computing offers scalable solutions, enabling businesses to manage large volumes of data without substantial infrastructure investments. Businesses can access real-time data, allowing for quicker decision-making and responsiveness to market demands.
Another significant advancement is the integration of the Internet of Things (IoT) within PIM systems. IoT devices can provide live data on products, enhancing inventory accuracy and reducing the chances of stockouts. This immediate access to product information influences purchasing and forecasting decisions.
The Role of AI and Machine Learning
Artificial Intelligence (AI) and Machine Learning change how PIM operates within inventory management. These technologies facilitate data analysis, identifying patterns in customer behavior and inventory trends that may not be evident to human analysts. Businesses can make more informed decisions based on predictive analytics, optimizing stock levels, and reducing excess inventory.
AI tools support automated classification and enrichment of product data. This increases data consistency and quality, ensuring that all product information is accurate and up-to-date. Additionally, AI can enhance personalization efforts. Tailoring product recommendations to individual customer preferences not only helps in managing inventory better but also increases overall customer satisfaction.
Evolving Consumer Expectations
Consumer expectations are continually evolving, and businesses must adapt accordingly. Today's consumers seek immediacy and personalization in their shopping experiences. PIM systems that provide accurate and timely product information are essential to fulfilling these expectations. Customers expect to find detailed speciation on products, including availability, specifications, and pricing.
Furthermore, transparency is increasingly critical. Consumers want visibility into product sourcing, information on sustainability, and ethical practices. PIM systems that enable businesses to showcase this information effectively will likely gain an advantage in the marketplace.
"Embracing these changes is not just about keeping pace; it is about staying ahead in a competitive market."
This proactive approach will ensure that businesses remain resilient and adaptable in the future.
Case Studies of Successful PIM Implementations
The relevance of case studies in understanding Product Information Management (PIM) cannot be underestimated. They provide concrete examples of how various industries successfully integrate PIM into their operational workflows to improve inventory management. This section discusses the practical applications of PIM, analyzing specific instances in the retail, manufacturing, and e-commerce sectors. By examining these case studies, businesses can glean insights into the tangible benefits of PIM and consider strategies for their own implementations.
Retail Sector Applications
In the retail sector, the integration of PIM has revolutionized the way businesses manage their product information. For example, a leading fashion retailer struggled with inconsistencies in product data across multiple sales channels. By adopting a centralized PIM system, they achieved higher data accuracy, reduced time spent on product updates, and streamlined the customer experience.
Key benefits observed include:
- Enhanced Product Data Consistency: Customers encounter the same product information regardless of the platform. This consistency builds trust and leads to higher conversion rates.
- Faster Time to Market: With streamlined product updates, merchants can introduce new items and sales promotions swiftly, keeping pace with market demands.
This case illustrates that effectively utilized PIM can lead not only to improved operational efficiency but also to better customer satisfaction and loyalty.
Manufacturing Case Studies
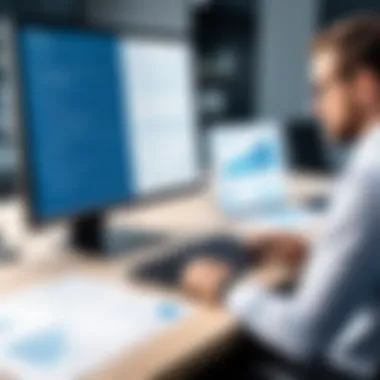
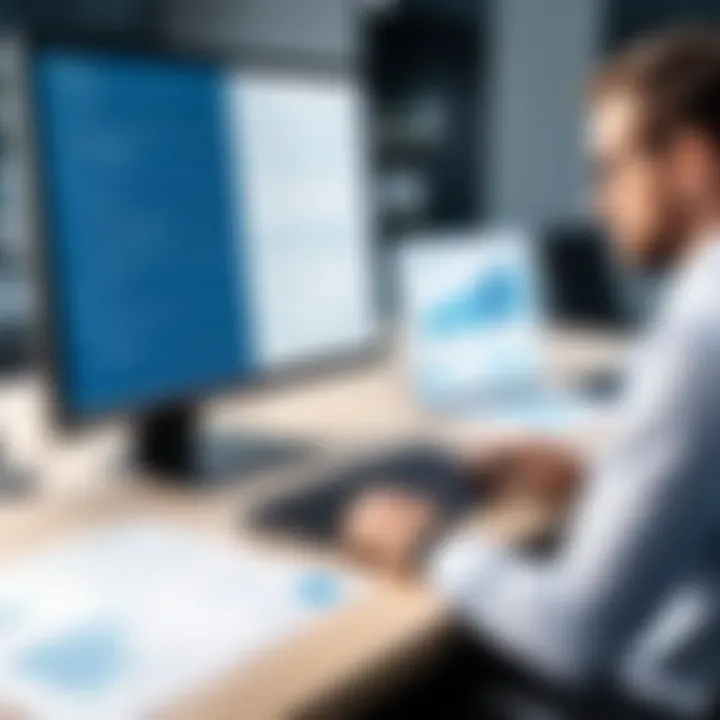
In manufacturing, effective PIM implementation can facilitate complexity in product information due to diverse suppliers and components. For instance, a prominent electronics manufacturer implemented PIM to manage its vast array of product specifications and compliance requirements. Before PIM, tracking changes across their extensive product lines was cumbersome.
Post-implementation, they reported:
- Improved Regulatory Compliance: Automated updates ensure that all product information adheres to industry standards, minimizing risks associated with compliance failures.
- Centralized Supplier Information: Access to updated data on suppliers helps in negotiating better terms and maintaining high standards.
The integration of PIM supports a smoother workflow, ensuring accurate data flows within the organization. This case exemplifies how PIM can mitigate risks and enhance control over essential product information required for manufacturing.
E-commerce Success Stories
The e-commerce sector presents unique challenges for PIM, especially with rapidly changing consumer preferences and expectations. A well-known online marketplace adopted a state-of-the-art PIM solution to address these challenges. They faced issues such as inconsistent product descriptions and slow updates across their extensive catalog. The decision to implement PIM yielded significant improvements.
Benefits observed include:
- Dynamic Pricing: Real-time data updates allow for agile pricing strategies tailored to consumer behavior, improving sales margins.
- Personalized Shopping Experience: With enriched product data, the marketplace offered tailored recommendations, resulting in higher customer retention and increased transaction values.
This success story underscores the critical role of PIM in adapting to rapidly shifting e-commerce landscapes. It provides evidence that PIM can act as a catalyst for driving sales and enhancing customer engagement.
"Implementing a PIM solution can lead to transformative changes in how businesses handle product data, optimize inventory, and satisfy customers effectively."
Through examining these diverse case studies, it becomes clear that PIM is not merely a tool but a strategic asset capable of driving significant operational improvements across various sectors. Businesses contemplating PIM implementations should consider the lessons learned from these industries.
Metrics for Measuring PIM Effectiveness
Measuring the effectiveness of Product Information Management (PIM) systems is crucial for any organization looking to optimize its inventory management. With the increasing reliance on data-driven decisions, understanding the right metrics is essential. These metrics not only gauge the performance of the PIM system but also help in identifying areas that need improvement. By focusing on specific elements, such as accuracy, turnover ratios, and customer feedback, businesses can ensure that their PIM strategies align effectively with their operational goals.
Data Accuracy Rates
Data accuracy is the backbone of any PIM system. High accuracy rates directly correlate with better decision-making, reduced operational costs, and enhanced customer trust. Accurate product data ensures that inventory levels are reflective of actual stock, minimizing issues such as overstocking or stockouts.
To calculate data accuracy, businesses can compare the number of correct data points against the total number of data points. A higher percentage indicates better performance. Here are some key considerations regarding data accuracy:
- Regular audits and updates to product information
- Implementation of data validation processes
- Employee training focused on data entry standards
Maintaining high data accuracy is not merely beneficial; it's critical for seamless inventory management. If the data informing inventory decisions is flawed, even the best PIM systems will not yield optimal results.
Inventory Turnover Ratios
Inventory turnover ratios are essential for understanding how efficiently a company moves its inventory. This metric indicates the number of times inventory is sold or used over a certain period. A higher ratio usually reflects effective inventory management that can directly benefit from PIM solutions.
Measuring inventory turnover involves the following calculation:
This ratio helps businesses to:
- Identify slow-moving products
- Optimize stock levels to reduce carrying costs
- Make informed purchasing decisions based on sales performance
When PIM systems offer accurate product information, it enhances the ability of businesses to monitor these ratios effectively, leading to better forecasting and inventory control.
Customer Satisfaction Scores
Customer satisfaction is a key determinant of a business's success. In the context of PIM, this metric assesses how well product information meets customer expectations. Accurate and comprehensive product information reduces confusion and increases trust, thereby contributing to an enhanced customer experience.
To evaluate customer satisfaction, organizations often use surveys or track Net Promoter Scores (NPS). It is crucial to:
- Solicit consistent feedback from customers about product data clarity
- Analyze complaints related to product discrepancies
- Act on customer insights to refine product data
By focusing on customer satisfaction scores, businesses leveraging PIM systems can refine their inventory management processes, ensuring that the right products are in the right locations, with accurate and clear information.
Improving these metrics not only leads to better internal outcomes but also fosters a stronger relationship with customers and enhances brand reputation.
Ending: The Essential Role of PIM in Inventory Management
The understanding of Product Information Management (PIM) is vital for effectively managing inventory. PIM serves as the backbone of product data management, ensuring that accurate and consistent information flows through various inventory systems. This article sheds light on the connection between PIM and inventory management, highlighting its critical benefits and considerations.
First, it is essential to recognize how PIM impacts inventory accuracy. By centralizing all product data, PIM minimizes errors that can occur from manual entries or fragmented data sources. This accuracy translates into improved inventory visibility, reducing the chances of overstocking or stockouts. Consequently, businesses can make informed decisions regarding their inventory levels, ultimately enhancing operational efficiency.
Moreover, PIM's role in integrating with supply chain processes cannot be overstated. It acts as a crucial link between various departments—such as sales, marketing, and supply chain management—ensuring that all stakeholders have access to up-to-date product information. These integrations allow for seamless inventory tracking, forecasting, and demand planning, which are essential for sustaining competitive advantages in today's fast-paced market.
"The effective integration of PIM with inventory management enhances decision-making processes across the organization."
Lastly, the adaptability of PIM solutions to meet evolving business needs means that as companies grow or pivot, their inventory management systems can evolve without disruption. This capability is particularly important for businesses that aim for scalability.
Synthesis of Key Points
In this discourse, several key points have emerged:
- Centralized Data Management: PIM ensures that data is stored in one location, improving accuracy.
- Enhanced Inventory Visibility: Real-time data enables better inventory tracking and management.
- Integration with Supply Chain: PIM connects various departments and improves workflow efficiency.
- Scalability: Adaptable PIM solutions can grow alongside a business, ensuring they remain relevant.
By focusing on these elements, organizations can harness the power of PIM to improve their inventory management strategies significantly.
Future Recommendations
Looking ahead, businesses should consider the following recommendations:
- Invest in Robust PIM Solutions: Selecting a PIM system that aligns with organizational needs will facilitate better data management and accuracy.
- Regular Training Sessions: Employees should be trained regularly to keep up with PIM best practices and updates.
- Continuous Performance Monitoring: Establish a system for periodic audits of PIM effectiveness and data quality.
- Leverage Emerging Technologies: As technologies like AI and machine learning evolve, integrating them with PIM can further enhance decision-making and inventory accuracy.
By implementing these strategies, organizations can maximize their PIM systems, leading to smarter inventory management practices.