The Impact of Manufacturing Execution Systems in Pharma

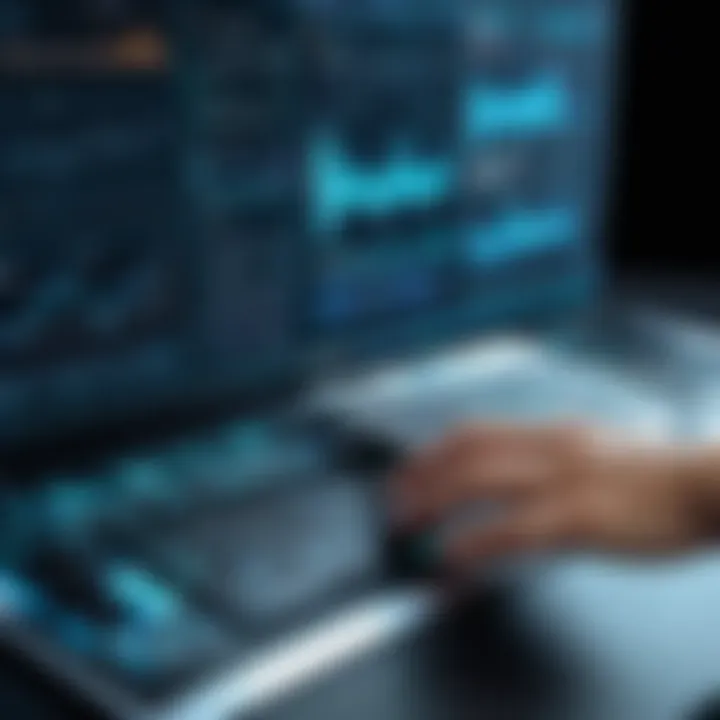
Intro
In the realm of pharmaceutical manufacturing, precision and compliance take center stage. The advent of Manufacturing Execution Systems (MES) marks a transformative shift in the way these industries operate. As organizations strive to enhance operational efficiency and meet the rigorous standards imposed by regulatory bodies, MES serves as an indispensable tool. This article provides an in-depth exploration of MES—its functionalities, system requirements, challenges, and future trends—tailored specifically for IT professionals and industry stakeholders.
Brief Description
Overview of the Software
At its core, a Manufacturing Execution System is designed to manage and monitor work in manufacturing. By bridging the gap between enterprise resource planning (ERP) and the shop floor, MES allows for real-time visibility into production. This capability is crucial for pharmaceutical companies where even minor deviations can result in severe issues, from product recalls to regulatory penalties.
Key Features and Functionalities
Below are several critical features that underscore the value of MES in the pharmaceutical industry:
- Real-Time Data Collection: MES can capture data from various machines and systems, ensuring all information is current and accurate. This reduces the risk of errors that might compromise production quality.
- Regulatory Compliance Tracking: The software facilitates adherence to industry regulations by automating compliance checks and generating necessary documentation.
- Production Scheduling: Enhanced scheduling capabilities allow companies to optimize their workflows, minimizing downtime and maximizing throughput.
- Quality Control: Integrated quality management tools ensure that every batch meets the necessary specifications, thereby maintaining product integrity.
"Manufacturing Execution Systems are the backbone of any effective pharmaceutical manufacturing operation, providing the visibility and control necessary to thrive in a complex regulatory landscape."
System Requirements
Hardware Requirements
For MES to function optimally, certain hardware specifications are necessary. Although these can vary, organizations generally need:
- A reliable server to host the MES software, capable of handling multiple user requests simultaneously.
- Workstations equipped with current operating systems to facilitate user access and interaction with the system.
- Network infrastructure that ensures secure and fast data transmission throughout the manufacturing plant.
Software Compatibility
Compatibility is a critical concern when integrating MES with existing systems. The following points should be kept in mind:
- Operating Systems: The MES must support the operating systems in use across the organization, whether it’s Windows, Linux, or another system.
- Integration with Existing ERP Systems: The ability to connect seamlessly with existing ERP solutions like SAP or Oracle is vital, as it allows for smooth data flows and unified operations.
- Data Standards: Support for industry-standard protocols such as ISA-95 can enhance interoperability with other manufacturing systems.
Preface to Manufacturing Execution Systems
Manufacturing Execution Systems (MES) have taken center stage in the realm of pharmaceutical manufacturing. In a sector that demands precision and strict adherence to regulatory standards, the role of MES cannot be overstated. These systems act as the backbone of operations, bridging the gap between enterprise-level data and the shop floor activities. With the right MES in place, companies can manage production more efficiently, respond to market demands faster, and maintain high levels of quality assurance.
One key benefit of MES is its ability to provide real-time visibility into production processes. For instance, manufacturers can monitor every stage of drug production, from the receipt of raw materials to packaging, allowing for immediate adjustments as needed. This level of oversight not only enhances operational efficiency but also minimizes waste and errors, which are crucial for maintaining compliance and meeting regulatory expectations.
Moreover, implementing an MES can facilitate better communication across departments. By centralizing data, stakeholders—from production managers to quality assurance personnel—can access the information they need to make informed decisions promptly. One could say it's akin to being given the blueprint of a building process; everyone knows where they stand and what needs to be done.
However, adopting an MES system is not without its challenges. Organizations need to consider existing infrastructures, employee training, and potential resistance to change when transitioning to a new system. Therefore, planning is essential for a smooth rollout.
As we examine the definitions and historical evolution of MES, it is vital to grasp not only how these systems function but also the context in which they have developed. Understanding this can shed light on why they have become indispensable in the pharmaceutical industry today.
Key Functions of MES in Pharmaceutical Manufacturing
The realm of pharmaceutical manufacturing is characterized by its stringent requirements for quality, efficiency, and compliance. In this environment, Manufacturing Execution Systems (MES) serve as pivotal tools that bridge the gap between production processes and enterprise-level planning. Their significance cannot be overstated; these systems not only facilitate real-time data management but also optimize operations, ultimately driving better outcomes.
Real-time Monitoring and Control
One of the standout capabilities of MES is its ability to provide real-time monitoring and control over manufacturing processes. Workflows in pharmaceutical production are complex and demand precise execution. Real-time monitoring empowers operators to oversee each step of production — from batch tracking to equipment status. By having up-to-the-minute data, decision-makers can quickly adjust parameters or troubleshoot issues.
Consider a scenario where a manufacturing line is producing a specific drug formula. If there’s a sudden fluctuation in temperature within a reactor, real-time alerts from the MES can prompt immediate corrective actions. This capability ensures that the quality of the final product remains uncompromised; quick responses can mean the difference between a successful batch and a hazardous one.
Furthermore, with control mechanisms integrated into MES, businesses can program automated responses to certain conditions, minimizing human error. This level of transparency and responsiveness builds a robust production environment that aligns with the pharmaceutical industry’s demand for reliability and efficiency.
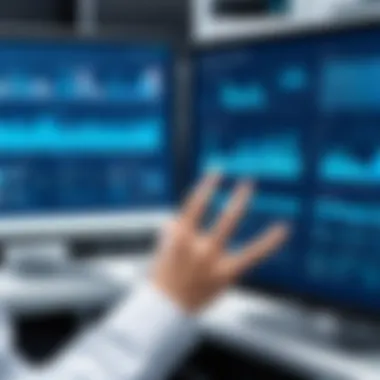
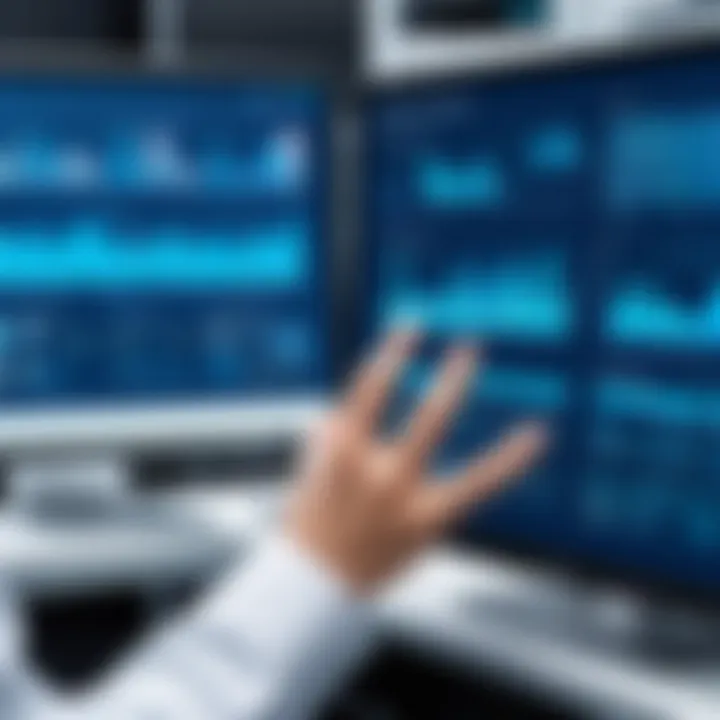
Data Collection and Analysis
Data, as the saying goes, is the new oil. In pharmaceutical manufacturing, data collection and analysis are cornerstones of effective MES implementation. These systems collect vast amounts of data generated during production, including quality metrics, operational performance, and regulatory compliance information. The challenge, however, lies not just in collecting this data but in making sense of it.
MES provides analytical tools that can sift through the noise and produce actionable insights. For instance, historical production data can highlight patterns, enabling predictive maintenance of equipment. If a machine tends to fail after a specific number of hours, the system can alert technicians for preemptive action, thereby reducing unexpected downtime.
Moreover, integrating data analytics into MES allows companies to enhance decision-making processes. With the right analytics, a pharmaceutical company might uncover hidden inefficiencies in its production line that, once addressed, could lead to significant cost savings and improved throughput.
Production Scheduling and Planning
Production scheduling and planning in pharmaceutical manufacturing are not trivial tasks. They involve intricate balancing of available resources, regulatory constraints, and market demand. MES plays a crucial role in streamlining these tasks.
Modern MES solutions offer advanced scheduling capabilities that can dynamically adjust to changes, be they internal shifts such as equipment failures or external disruptions like supply chain delays. These systems enable planners to visualize the entire production process, ensuring that every resource is utilized optimally and that production targets are met.
Another aspect worth noting is the integration of MES with other enterprise systems, such as Enterprise Resource Planning (ERP). This synergy allows for more coordinated planning across various departments. For example, if a new drug receives market approval, production schedules can be adjusted swiftly to meet customer demand, ensuring that the company stays competitive.
"MES acts as the nerve center of pharmaceutical production, orchestrating a symphony where every note must be played perfectly to ensure quality and compliance."
This orchestration of production processes not only leads to enhanced productivity and reduced lead times but also ensures a swift response to changing market conditions. The integration of MES into production planning frameworks is essential for any pharmaceutical manufacturer aiming for excellence in operational efficiency.
Integration Challenges with Existing Systems
The integration of Manufacturing Execution Systems (MES) into existing manufacturing environments, especially in the pharmaceutical industry, is crucial. As organizations strive for streamlined operations, understanding and overcoming the challenges in integrating MES with existing systems becomes a priority. These challenges can impact productivity and compliance, which makes addressing them a necessity.
Interfacing with Legacy Systems
Many pharmaceutical operations still rely on legacy systems, which may be outdated and not designed to connect easily with newer technologies like MES. These older systems often lack the flexibility needed for modern data requirements.
For instance, when a facility is using a custom-built manufacturing system, integrating MES can seem like trying to fit a square peg in a round hole. There are often compatibility issues that arise, such as differences in data formats and communication protocols. Adapting these legacy systems to communicate with MES requires careful planning and often tailored solutions that can be time-consuming and expensive.
One solution many companies find effective is employing middleware. Middleware can sit between the old and new systems, translating data and ensuring both can communicate effectively without a complete overhaul of existing platforms. This approach can help maintain the integrity of the original system while making necessary updates to integrate with the MES. Ultimately, a successful interface can enable better data flow, improving functionality across the board.
Data Silos and Information Flow
Data silos are another significant challenge in the integration process. In many organizations, information is often trapped in separate departments or systems and is not easily accessible. This disjointed information flow can hamper decision-making processes and impede overall efficiency.
For example, suppose quality control data exists in one part of the organization while production data is siloed in another. There can be significant delays in identifying production issues or ensuring compliance with safety standards. When MES is implemented correctly, it can break down these walls, allowing for real-time data access and improved decision-making.
Addressing data silos requires a cultural shift in how information is shared across departments. Encouraging an environment where collaboration is favored can significantly enhance the effectiveness of MES. Additionally, leveraging data integration tools can assist in creating a unified data platform, ensuring that information flows freely across all levels of the manufacturing operations.
Quality Management and Regulatory Compliance
In the pharmaceutical industry, where precision and safety reign supreme, the role of quality management and regulatory compliance cannot be understated. These aspects ensure that products meet stringent health and safety standards while adhering to the regulatory framework set by governing bodies. This section delves into the essential elements of quality management and how Manufacturing Execution Systems (MES) integrate into this framework, ultimately driving continuous improvement in production processes.
GxP Compliance Requirements
Good Practice (GxP) guidelines, encompassing Good Manufacturing Practice (GMP), Good Clinical Practice (GCP), and Good Laboratory Practice (GLP), lay the foundation for maintaining quality in pharmaceuticals. Compliance with GxP is not merely a matter of adhering to regulations; it signifies a commitment to ensuring that pharmaceutical products are safe, effective, and of high quality.
An MES equips pharmaceutical manufacturers to achieve and maintain GxP compliance through several mechanisms:
- Automation of Workflows: By automating standard operating procedures, an MES minimizes human error, which is essential for compliance.
- Validation Checks: Ongoing validation processes embedded within MES can regularly check whether operations meet GxP requirements, facilitating proactive adjustments as needed.
- Real-time Monitoring: Continuous monitoring allows for immediate detection of deviations from compliance, so corrective actions can be taken swiftly, keeping production aligned with standards.
Emphasizing GxP compliance not only reduces risks associated with product recalls and fines but also enhances the company's credibility within the market. It instills confidence in stakeholders, from regulatory bodies to the end consumers.
Audit Trails and Documentation
Another critical aspect of quality management in pharmaceutical manufacturing is maintaining comprehensive audit trails and documentation. Regulations mandate that every aspect of the production and quality control processes be documented to ensure traceability and accountability. MES systems are designed to facilitate rigorous documentation practices:
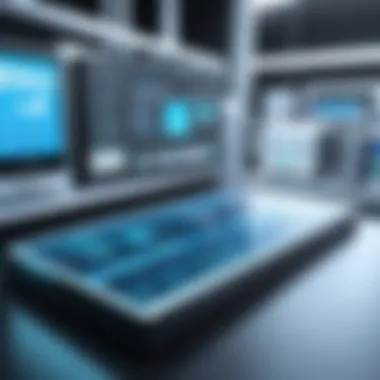
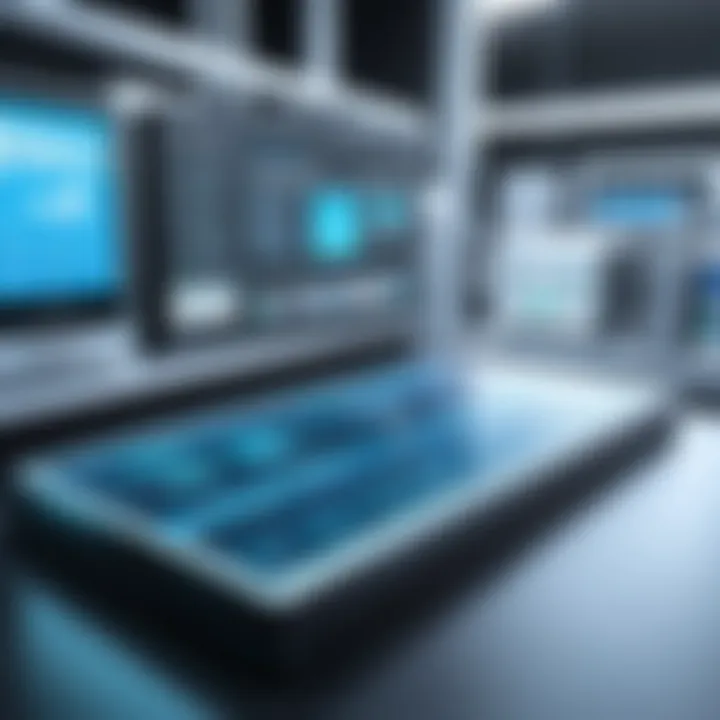
- Automatic Record Keeping: Every action taken within the MES is recorded automatically, creating an exhaustive account of every production cycle. This is vital during audits.
- Version Control: The system keeps track of changes made to documents and procedures, making it easier to refer back to previous versions if discrepancies arise.
- Easy Retrieval: In the event of an audit or inspection, having organized and accessible records ensures compliance is demonstrable, streamlining the process.
"In today's regulatory environment, the ability to provide clear, concise documentation can make or break a company's standing in the industry."
Enhanced documentation practices contribute significantly toward ensuring compliance and quality management. Companies can manage risks proactively, making necessary adjustments before problems escalate.
In summary, integrating quality management and regulatory compliance within MES not only supports compliance with GxP standards but also fosters a culture of quality that permeates every aspect of pharmaceutical manufacturing. Continuous advancement in these areas allows businesses to not just meet standards, but set them.
The Role of MES in Enhancing Operational Efficiency
In the pharmaceutical industry, MES plays a vital role in shaping how organizations manage their production processes. Operational efficiency isn’t just a buzzword; it is the lifeblood of a competitive enterprise. By effectively utilizing Manufacturing Execution Systems, businesses can not only streamline their workflows but also bolster overall productivity. Understanding how MES enhances operational efficiency is critical for any IT or software professional looking to make a tangible impact in their organization.
The importance of MES can’t be overstated. It bridges the gap between manufacturing and business operations, keeping everything in sync. This integration means real-time data flow from the shop floor to upper management, promoting faster decision-making and a more agile response to changes. Key areas where MES drives efficiency include:
- Real-time data access: By providing timely information, MES helps personnel to make informed decisions without delays.
- Process optimizations: Streamlined processes ensure resources are utilized effectively, minimizing waste and downtime.
- Regulatory compliance: Compliance often requires efficient procedures, which MES can facilitate, therefore reducing the likelihood of costly penalties.
"Operational efficiency isn’t just about doing things faster; it’s about doing them smarter."
Streamlining Production Processes
One of the core functions of MES in pharmaceutical manufacturing is the capability to streamline production processes. A well-deployed MES allows for the real-time monitoring of production lines, ensuring that any bottlenecks or irregularities are dealt with promptly. Rather than sifting through mountains of paperwork or outdated spreadsheets, operators can see everything unfold in real time. This proactive approach means:
- Reduced lead times: Quick adjustments to workflows can be made, which is essential in a sector where timing is often critical.
- Increased throughput: By optimizing flows—like balancing workloads or scheduling maintenance during downtimes—plants can ramp up production without compromising quality.
- Visibility: Having a clear view of every step in the manufacturing process allows for immediate responses to issues, preventing disruptions.
The devil is often in the details. Effective MES requires detailed mapping and understanding of each step of the production process. By accurately tracking every single component of the manufacturing journey, companies can pinpoint exactly where improvements can be made.
Reducing Downtime and Waste
Another significant advantage of MES involves its ability to minimize downtime and waste, two crucial elements that can drain resources and erode profits. The complexity of pharmaceutical production makes it easy for disruptions to lead to substantial financial losses. Hence, MES helps identify potential issues before they escalate. Strategies include:
- Predictive maintenance: Advanced MES can analyze machine performance and determine when maintenance is necessary, preventing unexpected breakdowns.
- Waste tracking: Monitoring usage of raw materials can help identify areas of waste, prompting process changes to minimize material loss.
- Data analysis: Analytics tools built into MES can examine past performances and suggest adjustments, leading to more efficient operations.
Both downtime and waste represent significant costs in pharmaceutical manufacturing. The implementation of an MES can drastically reduce these factors, reinforcing a company's bottom line while simultaneously enhancing productivity. For any aspiring professional in this field, grasping the intricacies of how MES contributes to operational efficiency is not just beneficial; it’s essential.
Case Studies of MES Implementation
Examining real-world case studies of Manufacturing Execution Systems (MES) implementation provides critical insights into their benefits and the pitfalls organizations might encounter. These narratives not only showcase how leading companies have harnessed the power of MES but also shed light on the considerations necessary to ensure a successful integration into existing systems. Understanding these scenarios allows IT professionals and businesses to glean practical knowledge about operational efficiency, compliance, and the overall enhancement of production processes.
Success Stories from Leading Brands
Several leading brands in the pharmaceutical sector have achieved remarkable results through the implementation of MES. For instance, Pfizer has reported significant improvements in production visibility since integrating MES into their operations. The system facilitates real-time monitoring of their manufacturing lines. With immediate access to data, production managers can make quick decisions to optimize workflows, resulting in a 30% reduction in product cycle time. This impressive achievement underscores the role of MES in enhancing responsiveness and agility within production processes.
Another notable case is Roche, which adopted MES to streamline its quality assurance processes. By employing electronic batch records, Roche not only sped up compliance checks but also improved the reliability of their documentation. Their return on investment (ROI) was evident through a substantial decrease in paper-related errors and a smoother audit process, leading to a 40% enhancement in operational efficiency.
Such success stories illustrate that when handled properly, MES can transform operational strategies, ultimately allowing businesses to maintain a competitive edge in the marketplace.
Lessons Learned from Failed Implementations
Not all MES implementations yield positive outcomes. Understanding the lessons from failed attempts is as crucial as celebrating successes. One example is Bristol-Myers Squibb, which faced challenges during its MES rollout. Due to inadequate user training and a lack of engagement from the workforce, the system faced significant resistance. The implementation, which aimed to streamline processes, ended up causing disruptions rather than improvements. The key takeaway here is that technology alone cannot drive change – human factors must also be considered.
Another cautionary tale involves Merck & Co., where an ambitious MES implementation resulted in unforeseen complexities related to data integration across various manufacturing plants. The lack of standardized data practices led to fragmentation, ultimately hindering data retrieval and analysis, which are vital for informed decision-making. Consequently, the company had to halt the project, incurring costs and delays.
The core of successful MES implementation lies not just in technology, but in an organization’s preparation, education, and adaptability.
These lessons emphasize the need for thorough planning, cross-departmental collaboration, and a focus on user training. Ensuring that all stakeholders understand the system’s benefits can significantly boost the chances of success.
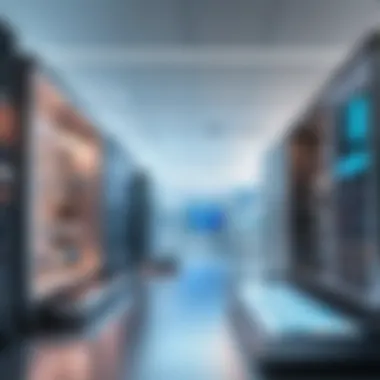
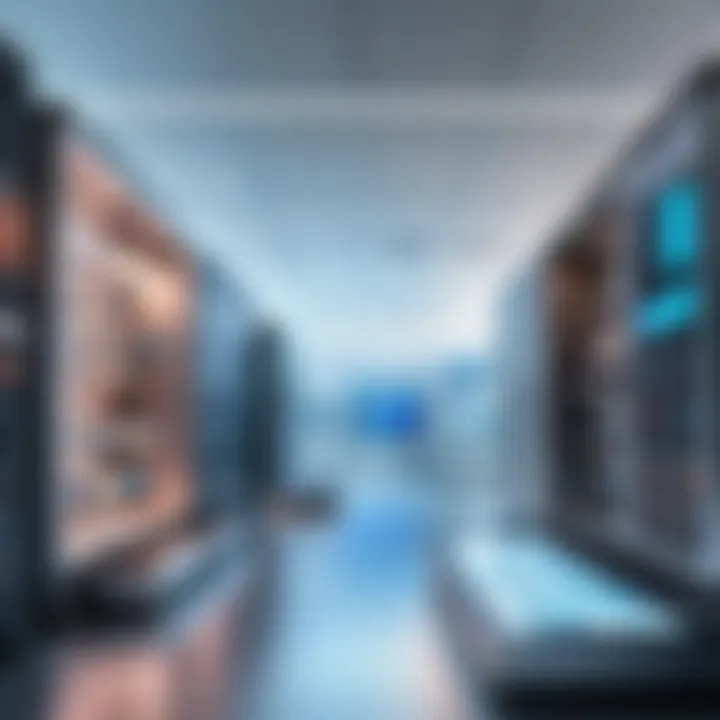
Emerging Trends in MES Technology
As the pharmaceutical industry continues to evolve, the role of Manufacturing Execution Systems (MES) is undergoing significant transformation. Staying abreast of emerging trends in MES technology is vital for organizations aiming to enhance efficiency, ensure compliance, and remain competitive in this fast-paced environment. Understanding these trends can offer businesses strategic insights into how to integrate advanced technologies and processes into their operations, ultimately leading to improved productivity and better resource management.
Cloud-Based MES Solutions
Cloud-based MES solutions have gained traction due to their flexibility and scalability. By utilizing the cloud, pharmaceutical companies can reduce the burden of local server maintenance and benefit from a pay-as-you-go pricing model. This allows for seamless updates and adaptability to changing needs. In a cloud environment, data accessibility becomes paramount. Staff can access real-time data from any location, which is increasingly important in today’s remote working culture.
Some notable benefits of cloud-based MES solutions include:
- Cost Efficiency: No heavy investments in infrastructure are needed, minimizing upfront costs.
- Flexibility: Easily scale services as business needs grow or shift.
- Faster Implementation: The deployment timeline is generally shorter than that for on-premises solutions.
- Enhanced Collaboration: Teams can work together effectively across various sites, sharing data and insights.
However, incorporating cloud-based MES also presents considerations. Data security is a primary concern, particularly in a heavily regulated market such as pharmaceuticals. Companies need to ensure that their cloud solutions adhere to stringent compliance standards, safeguarding sensitive information from cyber threats while maintaining efficiency.
Integration of IoT and MES
The integration of the Internet of Things (IoT) with MES represents a significant advance in pharmaceutical manufacturing. IoT devices can collect vast amounts of data from equipment and processes in real time, providing actionable insights that enhance decision-making. This synergy between IoT and MES allows for better tracking of production flows, inventory levels, and equipment status.
Emerging IoT technologies are becoming instrumental in automating repetitive tasks, which helps reduce human error. When paired with MES, the data from IoT devices can improve:
- Predictive Maintenance: Analyzing equipment data helps predict when maintenance is needed, minimizing downtime.
- Supply Chain Visibility: Real-time tracking increases transparency across all stages of production.
- Quality Control: Constant monitoring can detect abnormalities in processes, ensuring adherence to quality standards.
Yet, integrating IoT isn’t without its hurdles. Companies must navigate the complexities of installing and maintaining numerous connected devices, as well as addressing data management challenges stemming from the increased volume of information generated. Balancing the potential improvements in efficiency with the operational demands is key to a successful IoT integration.
"Integrating IoT with MES systems opens new doors for groundbreaking efficiencies, but achieving this integration requires thoughtful planning and execution."
Future Outlook: MES in Pharmaceutical Manufacturing
The landscape of pharmaceutical manufacturing is on the brink of transformation, with Manufacturing Execution Systems (MES) at the center of this evolution. The importance of this topic cannot be overstated, as MES holds the key to unlocking efficiencies and ensuring compliance in an increasingly complex regulatory environment. In the future, we can expect MES to harness advanced technologies that not only streamline production but also improve data integrity and operational transparency, thereby redefining best practices in the industry.
Predicted Developments and Innovations
As we look ahead, several developments are anticipated in the realm of MES, which promise to reshape pharmaceutical manufacturing. These innovations include:
- Integration with Artificial Intelligence (AI): By leveraging AI, MES can analyze vast amounts of production data in real time, leading to predictive insights that help in optimizing processes. For instance, AI algorithms could detect patterns in production inefficiencies, enabling proactive adjustments before issues arise.
- Blockchain for Traceability: The quest for quality and safety necessitates robust traceability of materials and processes. Blockchain technology could offer a decentralized and tamper-proof way of ensuring that every step in manufacturing is recorded systematically, thereby enhancing trust in product integrity.
- Enhanced User Interfaces: Future MES solutions are likely to employ user-centric design principles that facilitate easier access to critical data. Intuitive dashboards and enhanced visual representations of key metrics would empower operators and management alike.
- Mobile and Remote Access: With the rise of remote work, having mobile access to MES capabilities becomes invaluable. Imagine a scenario where production managers can oversee operations from anywhere, armed with real-time data updates and alerts about any deviations from standard processes.
- Smart Factory Integration: The future will likely see MES systems seamlessly integrating with Internet of Things (IoT) devices, allowing for unprecedented levels of real-time data collection and monitoring. Sensors on machines could report functional status directly to the MES, drastically reducing the time taken to identify and rectify issues.
"The integration of MES with emerging technologies will not only drive efficiency but also enforce a culture of continuous improvement within organizations."
Strategies for Continuous Improvement
Continuously enhancing the capabilities of MES is crucial for keeping pace with the dynamism of the pharmaceutical industry. Some key strategies include:
- Regular Training and Upskilling: As new functionalities and features are introduced, ongoing training programs must be established for employees. This ensures they are equipped to leverage the full potential of the MES.
- User Feedback Mechanisms: Creating channels for feedback from end-users can help identify pain points and enhancement opportunities. Utilizing surveys and regular check-ins can establish a continuous feedback loop.
- Benchmarking Performance: Regularly comparing performance metrics against industry standards can help organizations spot areas needing improvement. This process encourages a standards-based approach to performance management.
- Adopting Agile Methodologies: Embracing agile practices in MES implementation and upgrades allows for quicker adaptations to changing needs and technological advances. Being flexible can lead to continuous delivery of value.
- Investing in Research and Development: Allocating budgets specifically for R&D of MES technologies is critical. This helps organizations stay ahead of the curve and can lead to customized solutions addressing unique operational challenges.
In summary, the future outlook for MES in pharmaceutical manufacturing is bright and full of potential. By capitalizing on predicted innovations and embracing continuous improvement methodologies, organizations can position themselves for success in an evolving industry.
End
In the context of this article, drawing conclusions on Manufacturing Execution Systems (MES) in pharmaceutical manufacturing reveals their fundamental role in shaping how modern pharmaceutical companies operate. The significance of MES transcends mere software; it embodies a strategic approach to integrating technology with human practices, fundamentally enhancing the production value chain.
Reflecting on the Impact of MES
Reflecting on the impact of MES presents a multidimensional view. At its core, MES serves as the backbone of operational efficiency. By providing real-time data, it allows manufacturers to make informed decisions swiftly, optimizing production workflows. For example, when a batch of medication is under production, MES tracks every stage, from raw materials to the finished product. Through accurate monitoring, deviations from the protocol can be identified almost immediately, which is crucial for product quality and compliance with stringent regulations.
Moreover, MES enhances teamwork among different departments. Rather than working in silos, information flows freely across teams. This integrated approach not only boosts morale but also creates a collaborative atmosphere that drives innovation. It’s akin to an orchestra where each instrument plays its part harmoniously, producing a cohesive output that’s greater than the sum of its parts.
"The application of MES is not just a technological shift; it’s a cultural transformation within organizations, fostering agility and responsiveness."
Final Thoughts on Future Directions
Looking ahead, the horizon for MES in pharmaceutical manufacturing appears promising, with a host of emerging trends poised to redefine operational paradigms. One key element is the anticipated rise of intelligent automation. As Artificial Intelligence (AI) and Machine Learning (ML) continue to develop, their integration with MES will enhance predictive analytics, allowing for more proactive management of production processes.
Another aspect worth noting is the growing emphasis on sustainability. As environmental concerns take precedence, MES will likely evolve to support greener manufacturing practices by optimizing resource usage and minimizing waste.