Comprehensive Overview of Electronic QMS Software
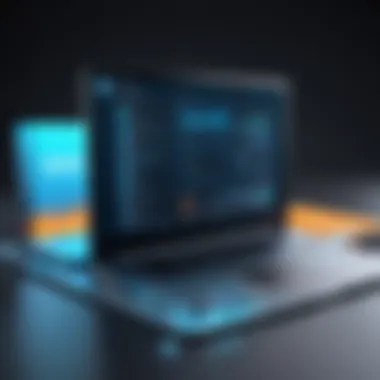
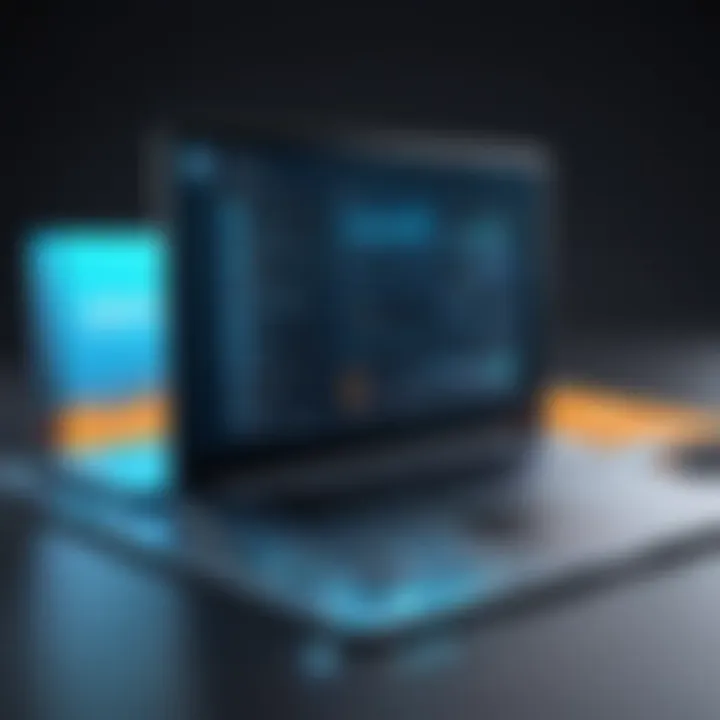
Intro
Quality management is essential in today’s business environment, more than ever before. Electronic Quality Management System (QMS) software plays a critical role in ensuring that organizations maintain high standards. This software helps in automating processes related to quality assurance, compliance, and overall product quality. In this guide, we will explore the significance of electronic QMS software, its key features, and how it can improve quality management in various sectors.
Brief Description
Overview of the software
Electronic QMS software offers systematic processes for managing quality across different departments within an organization. It centralizes quality-related information through digital management, replacing traditional paperwork, which can be cumbersome. This transition to electronic systems allows for better control of documents, audits, and compliance management.
Key features and functionalities
Some of the fundamental functionalities of electronic QMS software include:
- Document Control: Maintains accurate records of quality documentation to ensure compliance.
- Audit Management: Streamlines the audit processes, making it easier to track findings.
- CAPA Management: Allows for corrective and preventive actions to be easily documented and monitored.
- Training Management: Facilitates training and certification tracking of personnel, ensuring they are qualified for their roles.
- Reporting and Analytics: Generates comprehensive reports to analyze trends and assess the effectiveness of quality processes.
Overall, these features are designed to enhance not just compliance but also operational efficiency in organizations.
System Requirements
Hardware requirements
The hardware requirements for implementing electronic QMS software can vary based on the solution selected. Generally, a standard setup may include:
- A reliable internet connection.
- Servers with adequate processing power and storage capacity for data management.
Software compatibility
In addition to hardware, compatibility with existing systems is crucial. Most electronic QMS solutions are designed to work with major operating systems. They may also offer integrations with enterprise resource planning (ERP) systems, customer relationship management (CRM) solutions, and other critical software used within organizations.
This compatibility ensures a seamless transition to electronic management without disrupting existing workflows.
"Investing in electronic QMS software is not merely an organizational upgrade; it’s a commitment to quality that resonates throughout the enterprise."
Prelude to Electronic QMS Software
In a highly regulated environment, maintaining high standards of quality is crucial. The electronic Quality Management System (QMS) software emerges as a vital tool for organizations seeking to enhance their quality management processes. This section provides an overview of electronic QMS software, emphasizing its role and significance in today's organizational landscape.
Definition of Electronic QMS
Electronic QMS refers to a digital system designed to manage and streamline quality-related processes within an organization. It serves as a centralized repository for documentation, policies, and procedures, ensuring all employees have access to the latest information. Unlike traditional paper-based QMS, the electronic version automates tasks, minimizes errors, and facilitates smoother workflows. It incorporates various modules that address different aspects of quality management, including document control, audit management, corrective and preventive actions (CAPA), and training management.
Importance in Quality Management
The importance of electronic QMS in quality management cannot be overstated. Organizations face numerous challenges when it comes to maintaining compliance with industry standards. An effective electronic QMS enhances overall efficiency by providing tools that help in tracking and managing quality processes. This improves communication and collaboration within teams by ensuring that everyone is on the same page.
"An electronic QMS significantly reduces the time spent on manual tasks, allowing teams to focus on strategic initiatives."
Furthermore, electronic QMS facilitates real-time data access, enabling organizations to monitor key performance indicators and make data-driven decisions. This responsiveness is vital in industries where quality and compliance are paramount. Additionally, by centralizing data, electronic QMS supports better risk management and enables organizations to respond promptly to any quality issues.
Key Features of Electronic QMS Software
Electronic Quality Management Systems (QMS) have gained traction as organizations strive for improved standardization and compliance in their quality processes. Understanding the key features of these systems is essential for both IT and quality management professionals. These features play a critical role in enhancing not only operational efficiency but also the overall quality of products and services.
Document Control
Document control serves as a core foundation of electronic QMS software. It ensures that organizations maintain their documentation in an organized and accessible manner. With a centralized repository for documents, companies can manage version control effectively. This helps to track changes and ensures that all employees work with the most current data.
The electronic nature of document control aids in reducing the risk of human error and inefficiency associated with paper-based processes. Users can set alerts for when reviews or updates are due, ensuring timeliness.
Furthermore, a solid document control system supports compliance with regulations such as ISO standards, which demand that companies demonstrate proper documentation practices. This is especially important in industries like pharmaceuticals and manufacturing.
Audit Management
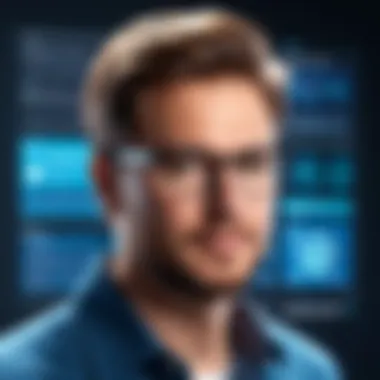
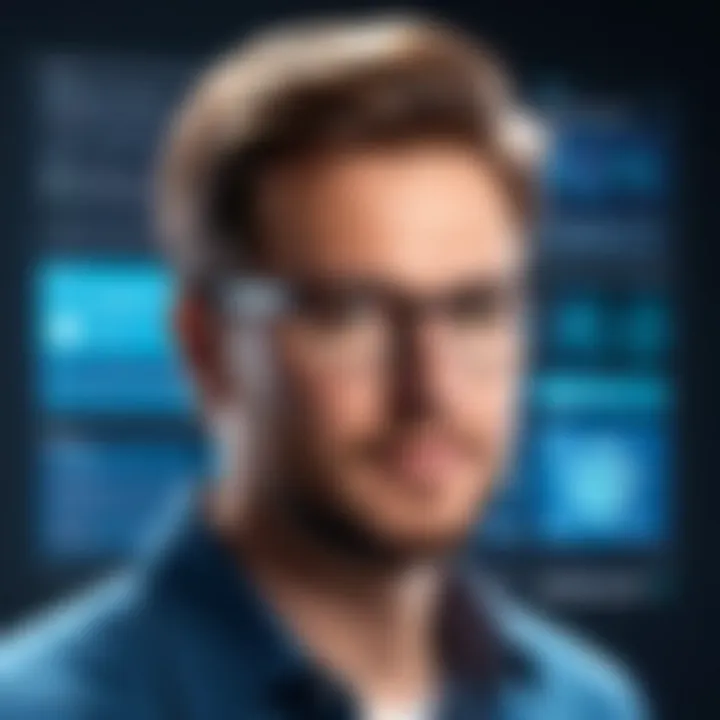
Audit management is another crucial feature of electronic QMS software. It allows organizations to streamline the audit process, making it more efficient and less time-consuming. Users can schedule audits, track findings, and generate reports easily within the system.
By having a digital audit trail, companies can easily retrieve historical data during internal or external audits. This transparency is vital for maintaining regulatory compliance and can prevent costly penalties. Additionally, automated reminders for upcoming audits ensure that nothing is overlooked.
CAPA Management
Corrective and Preventive Actions (CAPA) management tools are essential for addressing and mitigating issues as they arise. Electronic QMS software allows for the seamless initiation and tracking of CAPA processes. This includes documenting nonconformances, investigating root causes, and implementing solutions.
The ability to analyze past CAPA data can help organizations identify trends and proactively address potential quality issues. This data-driven approach fosters a culture of continuous improvement within the organization, leading to enhanced product quality.
Training Management
Training management features facilitate the systematic tracking of employee training and competency. Ensuring staff members are well-trained is fundamental to compliance and quality objectives. The software can maintain training records, monitor completion status, and identify gaps in skills.
Additionally, electronic QMS can automate reminders for training renewals, thus minimizing the risk of non-compliance due to lacking or outdated training. Enhanced training management ultimately leads to a more knowledgeable workforce, better equipped to adhere to quality standards and processes.
Risk Management
Risk management features in electronic QMS software enable organizations to systematically identify, assess, and mitigate risks that could impact product quality. This function is particularly relevant in industries that deal with stringent regulations and high stakes.
By employing tools for risk analysis, companies can use quantitative and qualitative methods to evaluate potential issues. Documenting risks effectively fosters a proactive culture of safety and compliance, as teams can act before problems escalate.
Benefits of Implementing Electronic QMS Software
Implementing electronic Quality Management System (QMS) software is a strategic move that can significantly benefit organizations across various industries. As companies continually strive for excellence, electronic QMS software plays a crucial role in enhancing operational effectiveness. By automating processes, ensuring compliance, and centralizing data, organizations can achieve better quality outcomes. The benefits highlighted below emphasize why investing in such systems is not only wise but necessary.
Improved Compliance
One of the main benefits of electronic QMS software is improved compliance with industry regulations and standards. Organizations must adhere to numerous guidelines, such as ISO 9001 and FDA regulations, to remain competitive and avoid penalties. Electronic QMS not only consolidates the requirements of these regulations but also streamlines compliance processes. This ensures timely audits and easier tracking of compliance-related documents. In summary, a well-implemented electronic QMS can significantly reduce the risk of non-compliance and enhance an organization’s reputation.
Enhanced Efficiency
Efficiency becomes a tangible advantage with the implementation of electronic QMS software. Traditional paper-based systems often lead to bottlenecks and delays in processes. Electronic QMS systems automate repetitive tasks, such as document routing and approval workflows. This automation results in reduced administrative burdens and leads to higher productivity levels. By enhancing efficiency, organizations can allocate more resources to core activities that drive growth and innovation.
Data Centralization
In many organizations, data exists in silos, making it difficult to access and analyze. Electronic QMS software centralizes quality-related data, enabling a single source of truth. This consolidation of information reduces redundancy and minimizes errors. Teams across various departments can access real-time data, fostering collaboration. With enhanced data visibility, organizations can monitor quality metrics and trends, leading to better strategic planning and operational adjustments.
Real-Time Reporting
The capability for real-time reporting is another important advantage of electronic QMS software. Quick access to data enables organizations to respond promptly to quality issues. Rather than waiting for periodic reviews, teams can generate reports at any time, offering insights into performance and compliance. This immediacy can be critical during audits or when addressing client queries. Ultimately, real-time reporting enhances transparency and accountability across the organization.
Informed Decision-Making
Informed decision-making relies heavily on accurate and timely data. Electronic QMS systems provide analytics and dashboards that empower managers and executives with insights on quality performance. With comprehensive reporting and data analysis, organizations can identify areas for improvement or innovation. Better decision-making leads to strategic advantages, enhancing overall quality and customer satisfaction.
"Effective quality management is not just about compliance; it’s about creating lasting value for an organization."
Selection Criteria for Electronic QMS Software
The decision to implement an electronic Quality Management System (QMS) software is pivotal for organizations striving to enhance their quality management capabilities. It is essential to carefully assess several criteria before making a selection. Each criterion plays a significant role in ensuring that the chosen solution aligns with the specific needs of the organization.
Scalability
Scalability is crucial when selecting electronic QMS software. This aspect determines whether the software can grow with your company. As businesses expand, they encounter new challenges and increased processes, making it necessary for the QMS to adapt. A scalable system allows organizations to add users, functionalities, or modules without a hitch. Consequently, it ensures that the quality management system remains effective as production increases or business requirements change. Without scalability, organizations may face limitations, potentially leading to inefficiencies in quality management.
User-Friendliness
User-friendliness is another key element in the selection process. An intuitive interface enhances user experience, which can significantly impact software adoption across the organization. If employees find the system difficult to navigate, they may resist using it, ultimately undermining its purpose. Hence, opting for an electronic QMS software that offers simple navigation, clear instructions, and responsive design is vital. The training effort required should also be minimal to ensure smooth onboarding. Improved user adoption translates to better communication, collaboration, and efficiency in managing quality processes.
Integration Capabilities
Integration capabilities are essential for an effective electronic QMS software. Organizations often use various systems across departments; thus, the ability to integrate smoothly with existing software tools is a must. This includes compatibility with ERP systems, CRM platforms, and other business applications. A robust QMS should facilitate data exchange, thereby eliminating data silos. Effective integration allows for better data analysis and reporting, ultimately leading to more informed decision-making regarding quality management. Companies should prioritize systems that support APIs and can work effortlessly with their infrastructure.
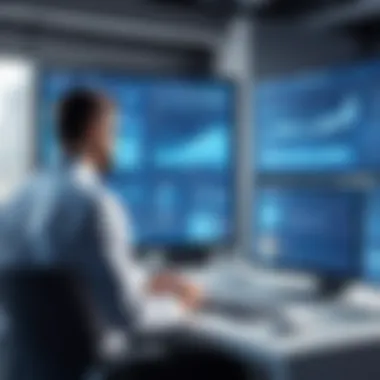
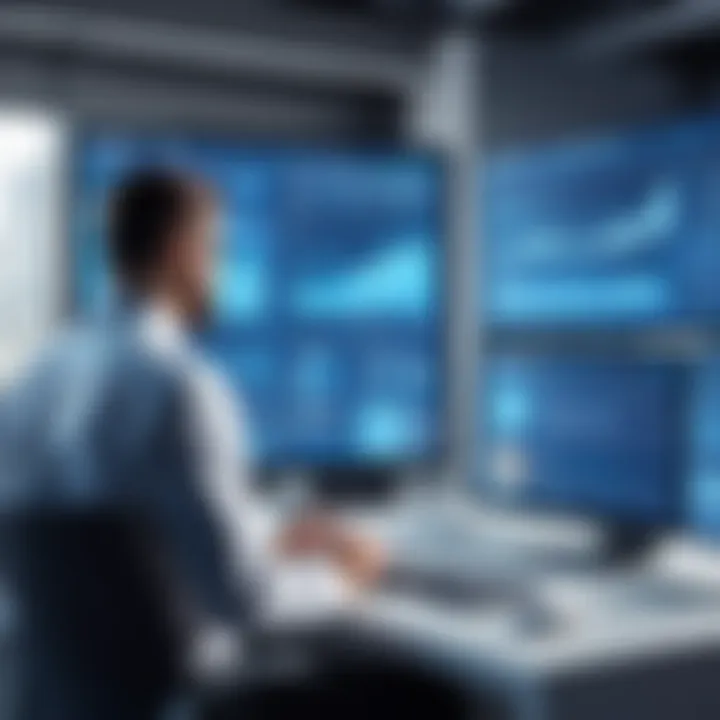
Support and Updates
The availability of ongoing support and regular updates should not be overlooked when choosing electronic QMS software. A reliable support system can be a lifesaver when technical difficulties arise or when users have questions about functionalities. Furthermore, regular updates ensure that the software remains compliant with changing regulations and possesses the latest features that enhance performance. Organizations should investigate what kind of support is offered—be it through a help desk, forums, or direct contact with software vendors—and how often updates are released.
Cost-Effectiveness
Finally, cost-effectiveness directly impacts the decision-making process concerning electronic QMS software. While price is an important factor, it should be evaluated in light of the total value provided by the system. Organizations might find it useful to compare upfront costs with long-term benefits, including savings from improved efficiency and better compliance. Additionally, hidden costs such as training, maintenance, and potential downtime during implementation should also be considered. A thorough cost analysis helps in selecting a solution that meets quality management needs while remaining within budget constraints.
Challenges in Implementing Electronic QMS Software
Implementing an electronic Quality Management System (QMS) can yield significant advantages for organizations, yet it is essential to be aware of the challenges that often arise during the transition. Identifying and addressing these challenges is critical for a successful implementation. In this section, we will explore five main issues often faced during the adoption of electronic QMS software. Understanding these challenges helps organizations prepare better, ensure smoother integration, and maximize the benefits that electronic QMS provides.
Resistance to Change
Resistance to change is a frequent hurdle in the implementation of electronic QMS software. Employees may be accustomed to traditional practices or manual systems. This familiarity creates a reluctance to adopt new processes. Organizations often notice skepticism among staff regarding the effectiveness of the new system, with many fearing that it may complicate their work rather than simplify it. To mitigate this, effective change management strategies should be in place. Involving employees from the start, providing clear communication about the benefits, and offering ongoing support can help to ease this transition.
Data Migration Issues
Data migration is another major challenge faced by organizations implementing electronic QMS software. Transitioning from old systems to a new platform often requires transferring large amounts of data. This process can be complex and time-consuming. Errors during migration can lead to incomplete or incorrect data, which in turn may compromise compliance and operational efficiency. To address these issues, organizations should plan the migration carefully, ensure thorough testing of the newly migrated data, and allocate resources specifically for data migration tasks.
Training Deficiencies
Training deficiencies present significant challenges when implementing electronic QMS software. Often, employees need proper training to utilize the new system effectively. If organizations do not provide adequate training resources, it may lead to low adoption rates. Lack of understanding can result in underutilization of the system, thus not delivering its full benefits. Organizations should prioritize comprehensive training programs. These programs can include hands-on sessions, user manuals, and ongoing assistance to ensure that all employees are confident in using the new software.
Compliance Gaps
Compliance gaps are also a concern in electronic QMS implementation. Organizations must ensure that the new system aligns with industry standards and regulations. If not, they may face serious consequences, including legal penalties or damage to their reputation. It is crucial to conduct a thorough assessment of compliance needs before implementing the software. Engaging with legal experts during the process can help identify potential gaps and ensure the system adheres to necessary regulations.
Ongoing Maintenance Needs
Finally, the ongoing maintenance needs of electronic QMS software should not be overlooked. After successful implementation, organizations need to maintain the software regularly. This includes system updates, bug fixes, and user support. Without proper maintenance, the software could become outdated, leading to performance issues or security vulnerabilities. Organizations should allocate resources and define a clear maintenance plan as part of their overall strategy to ensure the long-term success of their electronic QMS.
Regulatory Considerations for Electronic QMS Software
Regulatory considerations are paramount for organizations that utilize electronic Quality Management System (QMS) software. These guidelines ensure that the software complies with industry standards and supports the organization's commitment to quality. Regulatory compliance impacts various areas, including product quality, safety, and operational integrity. Recognizing and understanding these regulations not only mitigates risk but also enhances credibility with customers and stakeholders.
Industry Standards
Industry standards serve as benchmarks for quality management practices, guiding organizations in the implementation of effective processes.
ISO
ISO 9001 is one of the most widely recognized international standards for quality management systems. It focuses on meeting customer expectations and delivering customer satisfaction. A key characteristic of ISO 9001 is its process approach, which promotes continuous improvement. This standard is beneficial because it provides a clear framework for managing quality and is applicable to any organization, regardless of size or industry.
The unique feature of ISO 9001 lies in its emphasis on customer feedback and satisfaction, helping organizations to align their processes with customer needs. However, its broad nature could lead to challenges in specific industries that require more stringent controls.
FDA Regulations
FDA regulations specifically apply to organizations in the medical, pharmaceutical, and biotechnology sectors. These regulations ensure that products are safe and effective for public use. The key characteristic of FDA regulations is their stringent requirements for documentation, validation, and compliance testing, which are critical for protecting consumers.
The unique feature of FDA regulations is their focus on formalized quality control procedures. While this ensures high standards, it can also create significant administrative burdens for organizations striving to maintain compliance while keeping up with product innovation.
ISO
ISO 13485 is specific to medical devices and addresses the requirements for a QMS where an organization needs to demonstrate its ability to provide medical devices that meet both customer and regulatory requirements. This standard is particularly beneficial for companies in the healthcare sector, as it offers clear guidelines tailored to their unique compliance needs.
The unique feature of ISO 13485 is its rigorous process documentation and risk management focus. This standard greatly enhances an organization’s credibility in the medical device field, but the detailed processes may require more resources to implement effectively.
Compliance Requirements
Compliance requirements are essential for ensuring that electronic QMS software fulfills legal and industry obligations. These requirements vary across sectors but often include data security, software validation, and training records. Non-compliance can lead to severe consequences, including fines and damaged reputations. Organizations must keep abreast of applicable regulations to ensure that their electronic QMS software remains compliant and effective in supporting quality management initiatives.
Maintaining regulatory compliance in the use of electronic QMS software is not merely an option; it is a necessity for sustaining quality and operational integrity within any organization.
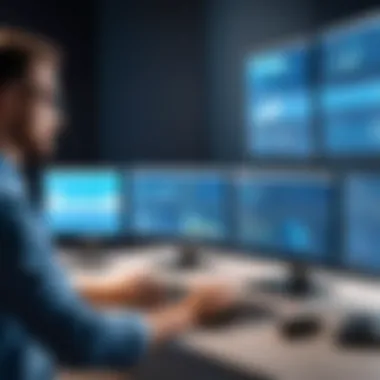
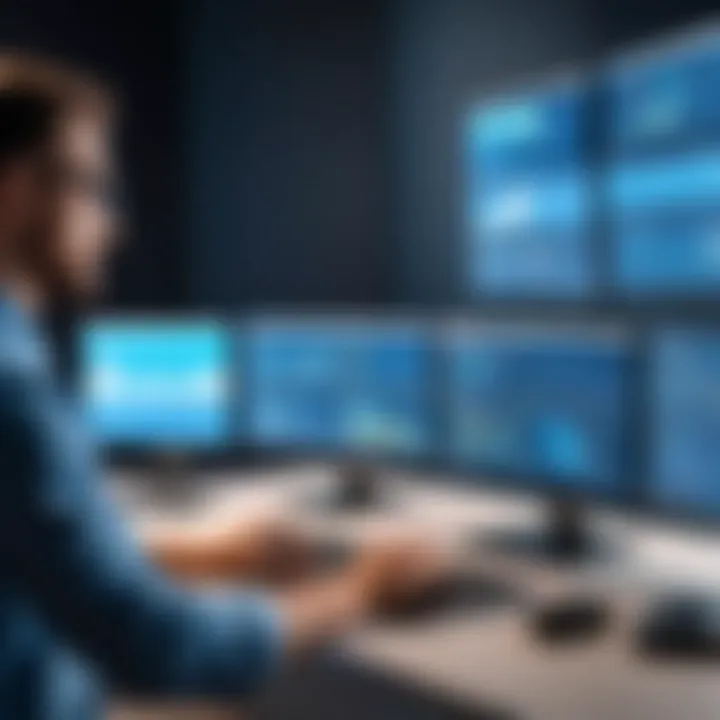
Future Trends in Electronic QMS Software
The electronic Quality Management System (QMS) software landscape is evolving rapidly. Innovations in technology are forging new paths for quality management processes. Understanding these trends is crucial for organizations aiming to stay competitive. These advancements not only enhance efficiency but also improve compliance and decision-making capabilities. Exploring future trends allows businesses to better harness QMS technology for their needs.
Artificial Intelligence Integration
The integration of Artificial Intelligence (AI) into electronic QMS software is poised to revolutionize the way organizations manage quality. AI can analyze vast sets of data much quicker than traditional methods. This capability enables predictive analytics, allowing companies to foresee potential issues before they arise.
Organizations can utilize AI to automate routine tasks, freeing up valuable time for staff to focus on more strategic functions.
Additionally, AI enhances compliance efforts. It helps in monitoring regulatory changes and assessing quality processes. Combining AI with QMS can lead to smarter, data-driven decisions that nurture quality improvements.
Cloud-Based Solutions
Cloud-based solutions represent a significant shift in how electronic QMS software is deployed. Businesses are increasingly adopting cloud technologies for their flexibility and scalability. Storing data in the cloud allows easy access from various locations, which is essential for remote workplaces.
These solutions are cost-effective because they eliminate the need for extensive hardware and maintenance. Furthermore, updates are regular and applied automatically, reducing downtime.
Companies can benefit from enhanced collaboration as teams on different sides of the world can share information effortlessly. Cloud solutions also support greater data security compared to traditional systems, making them an attractive option for many organizations.
Enhanced Analytics Capabilities
Analytics play a crucial role in any effective QMS. The future of electronic QMS software includes enhanced analytics capabilities that enable organizations to derive deeper insights from their quality data. Advanced analytics tools can spot patterns and trends that may not be visible on the surface.
With these capabilities, companies can track their performance metrics over time, identify areas for improvement, and gauge the effectiveness of their quality initiatives. As organizations increasingly rely on data to make informed decisions, the demand for robust analytical features in QMS will only grow.
Mobile Accessibility
The rise of mobile technology is also transforming electronic QMS software. Mobile accessibility allows users to interact with the system from various devices such as smartphones and tablets. This accessibility supports on-the-go compliance and allows quality personnel to perform audits and document issues immediately.
With mobile solutions, teams can collaborate in real time. Staff can enter issues as they occur, leading to faster resolution rates. Ultimately, mobile accessibility enhances responsiveness and streamlines quality management processes.
The future of electronic QMS software is aligned with technological advancements, such as AI and mobile solutions, which significantly impact how organizations manage their quality processes.
Case Studies: Successful Implementation of Electronic QMS Software
The exploration of case studies regarding the implementation of electronic QMS software provides a practical perspective on how these systems influence various industries. These real-world examples highlight not only the operational adjustments companies make but also the resultant efficiencies and compliance achievements. By analyzing these scenarios, organizations can grasp the tangible benefits and considerations necessary for cultivating an effective quality management culture.
Case Study One: Pharmaceutical Industry
In the pharmaceutical sector, compliance with strict regulatory standards is non-negotiable. A prominent pharmaceutical company adopted an electronic QMS to streamline its operations and enhance compliance. The integration of the software eliminated manual processes that were prone to errors.
The results were significant. By automating document control and audit procedures, the company improved its audit readiness and data integrity. This system enabled real-time tracking of CAPAs (Corrective and Preventive Actions) and facilitated better training management for employees. The software also provided comprehensive reporting capabilities, which proved critical during regulatory inspections. The electronic QMS effectively contributed to a culture of quality, allowing the company to maintain adherence to FDA regulations while also expediting product development cycles.
Case Study Two: Manufacturing Sector
In the manufacturing domain, an electronics manufacturer faced challenges regarding product quality and compliance. The management decided to implement an electronic QMS to enhance overall process efficiency. This decision stemmed from the need to reduce waste and infuse consistency throughout the production lines.
The implementation yielded impressive results. The centralization of quality-related data minimized the risk of inconsistencies and improved decision-making. Additionally, the software’s risk management functionalities allowed the company to proactively identify potential issues in production, thus mitigating risks before they escalated. Employee training became more structured, ensuring that workers were equipped with the knowledge necessary to uphold quality standards. Ultimately, the manufacturer saw decreased downtime and lower defect rates, which significantly boosted their market reputation.
Case Study Three: Food and Beverage Industry
In the food and beverage sector, maintainng quality standards is critical to both consumer safety and regulatory compliance. A popular food processing company faced numerous quality assurance challenges. The management opted for an electronic QMS in response to these issues, aiming to renovate their quality management processes.
This transition underscored the importance of traceability and compliance. The electronic QMS system implemented allowed for detailed tracking of ingredients, process controls, and environmental factors affecting production. Furthermore, audit management capabilities streamlined the internal inspection process, leading to faster identification of potential compliance issues. The software also facilitated user-friendly access to training materials, ensuring all staff adhered to the best practices in food safety and quality assurance.
Culmination
In summarizing the comprehensive insights gathered throughout this article, we establish the role of electronic Quality Management System (QMS) software as more than just a tool. It serves as a critical component in the evolution of quality management processes across various industries. As organizations strive for excellence and compliance, understanding the key elements discussed is essential for informed decision-making.
Summarizing Key Insights
The integration of electronic QMS software offers numerous advantages that directly impact operational efficiency and regulatory compliance. Key insights include:
- Enhanced Compliance: Electronic QMS assists businesses in adhering to industry standards and regulations, reducing risks of non-compliance.
- Improved Efficiency: Automatic workflows streamline processes, allowing teams to focus on higher-value tasks, leading to better productivity.
- Centralized Data: A robust system centralizes documentation, making data easily accessible and reliable for decision-making processes.
- Real-Time Reporting: The ability to generate reports quickly allows organizations to identify issues and take corrective actions swiftly.
These insights reinforce that electronic QMS software is an investment in operational integrity and quality enhancement.
Looking Ahead in Quality Management
As we look to the future of quality management, several trends show promise for evolving electronic QMS systems. Key considerations include:
- Artificial Intelligence: The integration of AI can facilitate predictive analytics, allowing organizations to anticipate quality issues before they arise.
- Cloud-Based Solutions: The shift towards cloud storage empowers organizations with the flexibility to access QMS solutions from anywhere, enhancing collaboration.
- Mobile Accessibility: As employees increasingly work remotely, having mobile access to QMS platforms will become a necessity, ensuring quality oversight regardless of location.