Creating 3D Models for Printing: A Complete Guide
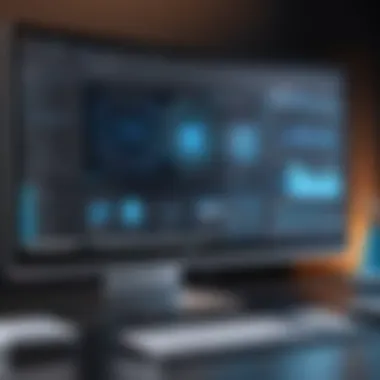
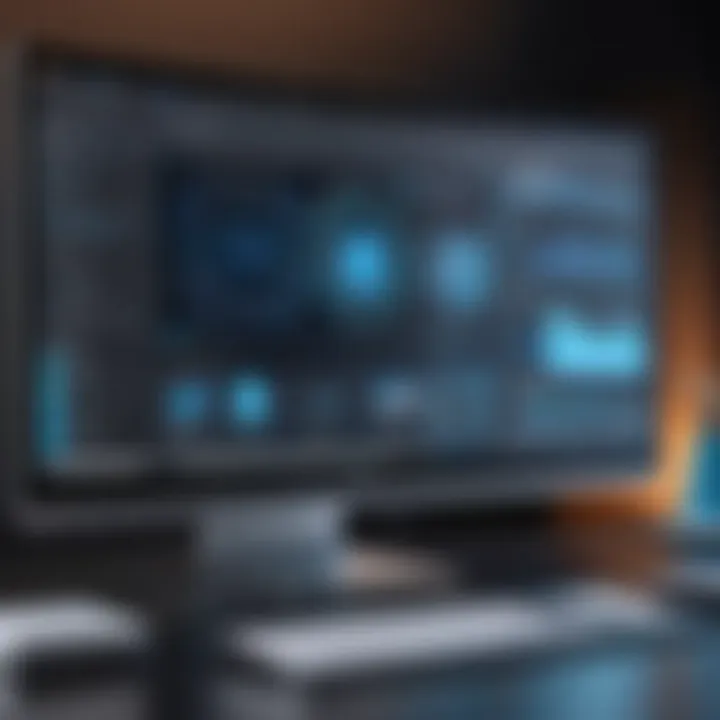
Intro
Creating a 3D model for printing is a journey filled with creativity and technical wizardry. For both newcomers and seasoned professionals, knowing the in-and-outs of this process is crucial. It’s not just about having the right tools but also understanding the context and applications of what you’re building.
Imagine the satisfaction of seeing your digital design transformed into a physical object, be it a prototype, a personalized gift, or a functional part. It’s a thrill akin to watching a puzzle come together, where each piece is your design's manifest components. This guide aims to clarify the maze of techniques, software, and systems that underpin successful 3D modeling, focusing on both the essential nuts and bolts as well as more nuanced considerations that can elevate your work.
Brief Description
In this world of 3D modeling, choosing the right software can make all the difference. The tools at your disposal can range from beginner-friendly applications designed for playful exploration to complex systems tailored for high-end modeling. Understanding these options enables you to select software that best aligns with your goals and capabilities.
Overview of the software
Various platforms exist that cater to different skill levels and requirements. Programs like Blender offer a comprehensive suite for 3D modeling, animation, and rendering, while Tinkercad simplifies the process for those just starting out. Then there’s Fusion 360, which strikes a balance between usability and advanced features, catering well to both hobbyists and professionals.
Key features and functionalities
When diving into 3D modeling software, keep an eye out for the following features:
- Intuitive User Interface: A well-designed UI can save you from frustration.
- Modeling Tools: Look for tools that allow for both parametric and direct modeling.
- Export Options: Ensure the software can export in formats compatible with 3D printers like STL or OBJ.
- Community and Support: Robust forums and documentation can be lifesavers when you hit roadblocks.
"A good 3D modeling software should feel like an extension of your own creativity, not a hurdle on the path to bringing your ideas to life."
System Requirements
Before diving into the modeling aspect, it’s wise to consider the technical landscape where your 3D journey will unfold. Different software has its own set of system requirements.
Hardware requirements
Depending on the complexity of your models and the software you choose, your hardware needs can vary widely. A modest setup may suffice for basic tasks, but if you’re venturing into intricate designs, consider the following:
- Processor: A multi-core processor will handle more demanding workloads.
- RAM: 16 GB or more is recommended for smoother multitasking.
- Graphics Card: A dedicated GPU can significantly enhance rendering performance.
- Storage: Opt for SSDs to decrease load times, particularly with larger files.
Software compatibility
Verify that your chosen software aligns with your operating system. Many popular applications are available on Windows and macOS, but others might only run on one of these platforms. Some software is even web-based, eliminating this concern altogether, but may come with restrictions on performance or additional features.
With a strong grasp of the tools and technologies behind 3D modeling, you can forge ahead. Keep reading to uncover detailed techniques and practical advice that can help turn your ideas into tangible realities.
Understanding 3D Printing
Understanding 3D printing is fundamental for anyone looking to create models tailored for this technology. The significance extends beyond merely knowing how to print something; it encompasses a broad comprehension of the processes involved, the materials used, and the potential of what can be achieved. In today’s world, where rapid prototyping and customization are in demand, grasping the nuances of 3D printing can set you apart in a competitive landscape. As we journey through this section, we’re going to break down what 3D printing really entails and how it plays a pivotal role in the modeling process.
Definition and Overview of 3D Printing
Put simply, 3D printing is a method of making three-dimensional solid objects from a digital file. The process is also known as additive manufacturing because it involves adding material layer by layer to create an object. Unlike traditional subtractive manufacturing, where material is removed from a block, 3D printing builds up a form, allowing for intricate designs and complex geometries that may not be attainable through conventional techniques.
3D printing involves several steps:
- Design: First, you create a 3D model using specialized software. This serves as the blueprint for the object.
- Slicing: The model is then sliced into layers using slicing software, optimizing it for the printer.
- Printing: The printer lays down material layer by layer, following the directions provided by the sliced model.
- Post-processing: This involves finishing the printed object, which can include removing supports and smoothing surfaces.
This definition captures the essence of 3D printing, but the true magic lies in its ability to transform digital designs into tangible products, thus bridging the gap between imagination and reality.
Applications of 3D Printing
The applications of 3D printing span across various industries, each harnessing its unique capabilities. Below are some prominent examples:
- Prototyping: Designers can quickly create prototypes to test ideas, reducing time from concept to completion. This is especially beneficial in industries like automotive and aerospace, where testing can be extensive and costly.
- Medical: Custom prosthetics, dental implants, and even bioprinting tissues are revolutionizing healthcare. 3D printing allows for personalization, improving patient outcomes significantly.
- Architecture: Architects can create intricate models that showcase designs in a physical form, facilitating better understanding among stakeholders.
- Consumer Products: From toys to home goods, 3D printing can produce low-volume custom products economically.
- Fashion: Designers are exploring 3D printing to create unique clothing, accessories, and footwear that challenge traditional manufacturing methods.
"The beauty of 3D printing is not just in its ability to create but in its flexibility to innovate across various fields."
As you can see, 3D printing isn't just a singular technology but a vast ecosystem that enhances creativity and efficiency in various sectors. Understanding its definition and applications equips one with the knowledge necessary to make informed decisions in modeling and printing their designs.
The Importance of 3D Modeling in 3D Printing
3D modeling holds a pivotal place in the 3D printing ecosystem. Every intricate detail you design in the digital space translates into the physical world, making the modeling phase not only a creative outlet but also a critical step in ensuring the final product meets your expectations. Simply put, the quality of the resulting print is directly tied to how well the model is crafted. With that in mind, let’s delve into the key aspects of why 3D modeling matters when it comes to 3D printing.
Transforming Ideas into Digital Formats
The process of transforming a concept into something tangible begins with 3D modeling. Think of it this way: your idea is like clay waiting to be sculpted. Every curve and contour of your design needs to be accurately represented in the digital realm. This transformation is not merely about replication; it’s about interpretation.
Sketching ideas on paper can only go so far. Once you dive into a modeling software, the possibilities expand. You have the ability to manipulate shapes, play with textures, and understand dimensions—something that paper never fully captures. For instance, creating a prototype for a machine part requires precise calculations, which can be done through modeling. A common mistake here is underestimating the complexity involved in this digital design. Being able to visualize your idea on screen allows you to spot design flaws before they reach the printer—saving time and material.
"The digital model is the blueprint for creation. Get it right, and you set the stage for success in printing."
Furthermore, 3D modeling enables iterative design processes. You can mock up multiple versions of a concept and refine them rapidly without the constraints associated with traditional manufacturing processes. This flexibility means you can engage in trial and error, moving blocks around or reshaping parts until they fit perfectly. For example, if you're designing an architectural model, adjustments become much simpler to execute digitally than they would be on a physical representation.
Impact on Print Quality and Accuracy
Once the model is created, the quality of that model plays a crucial role in the resulting printed object. Any detail that is overlooked or inaccurately designed in the 3D model may lead to defective prints. Too thin a wall, for instance, can cause breakage during printing; too thick can waste material and time. Understanding the design intricacies is essential.
A poorly designed model might result in frustrating issues during printing such as warping, inaccuracies in size, or the need for excessive support structures. Every layer printed is a reflection of what was crafted in the digital space. The more meticulous the modeling, the better the print—this is a tenet every designer and engineer should keep close to their heart.
Consider these key factors that impact print quality:
- Wall thickness: Ensuring appropriate thickness prevents structural weaknesses.
- Detail resolution: Higher detail results in better surface finish and accuracy.
- Dimension accuracy: Any miscalculation can result in parts that don’t fit or function as intended.
Choosing the Right Software for 3D Modeling
Selecting the appropriate software to create 3D models is a pivotal step in the 3D printing process. With a variety of options available, both free and paid, it can be bewildering to find the right fit for your specific requirements. Software capabilities can significantly impact your modeling speed, the quality of your designs, and ultimately, the efficiency of your entire workflow. It's essential to weigh options based on user skill level, intended application, compatibility with printing hardware, and the specific features offered.
Free Software Options
Free software can be an excellent starting point for beginners or those experimenting with 3D design without upfront investment. Here are a few notable tools:
- Tinkercad: A browser-based 3D modeling tool ideal for beginners, easy to navigate with drag-and-drop functionality.
- Blender: A powerful open-source software that caters to both simple and advanced users, great for more complex modeling tasks.
- FreeCAD: As the name suggests, it is free and focuses on parametric modeling, making it suitable for technical and engineering applications.
Each tool has its learning curve, but they provide ample resources online to help get you started. It would be wise to consider what you hope to achieve with your projects when selecting free software.
Paid Software Solutions
While free options abound, investing in paid software often provides advanced functionalities that can save time and enhance design quality. Some noteworthy paid solutions include:
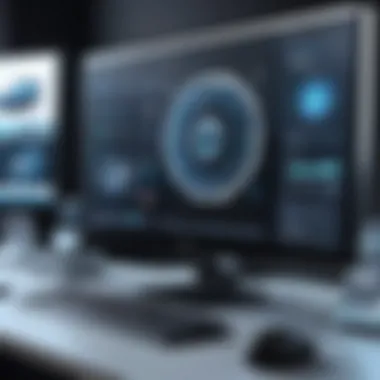
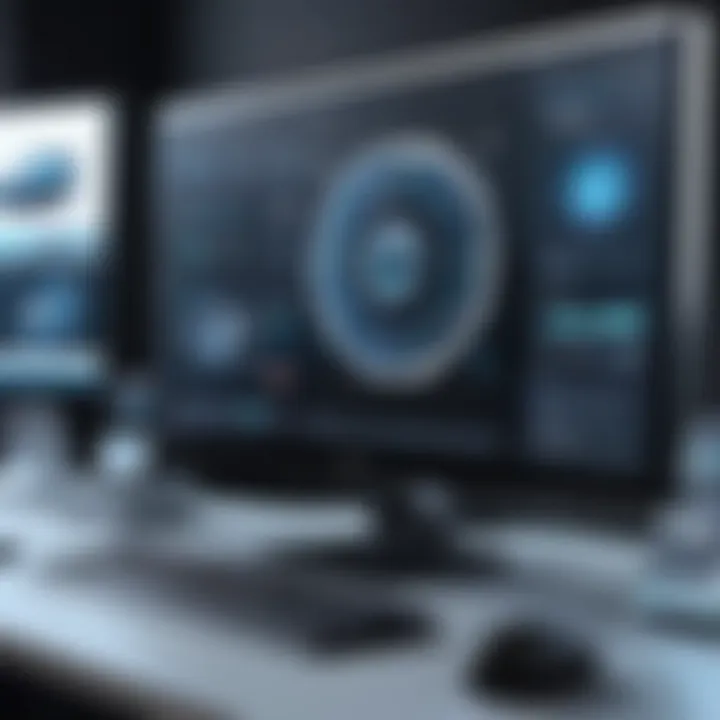
- Autodesk Fusion 360: Widely praised for its versatility and comprehensive features, suitable for everything from industrial design to mechanical engineering.
- SolidWorks: This software is the gold standard for engineering and product design, offering robust simulation and validation capabilities.
- Rhinoceros: Known for its powerful modeling capabilities, especially for organic shapes and complex geometries.
Utilizing paid software often comes with customer support and ongoing updates, which can be invaluable as technology and trends evolve.
Factors to Consider in Software Selection
When choosing software, several considerations come into play:
- Skill Level: Beginners might want to stick to user-friendly platforms, while advanced users might find complex tools more advantageous.
- Project Requirements: Certain software excels in specific areas. If you need precise engineering models, software designed for CAD applications might be your best bet.
- Community and Support: An active user community can be a repository of information and solutions. Check forums or platforms like Reddit for user experiences and recommendations.
- Compatibility: Ensure that the software you choose is compatible with your 3D printer and the file formats you plan to work with.
"The right software can transform your 3D printing experience, turning an idea into a functional model with clarity and precision."
Fundamentals of 3D Design
When diving into the world of 3D modeling, grasping the fundamentals is crucial. This foundation paves the way for creating complex models that not only function correctly but also look appealing. Understanding basic shapes and geometric concepts lays the groundwork for more advanced modeling techniques. Without a solid grasp of these core elements, even experienced designers might find themselves in a pickle when tackling intricate projects.
Overall, the importance lies in how these basic principles can empower designers. By mastering them, you're better equipped to manipulate 3D forms, experiment with various designs, and ultimately produce models that stand out. This section will explore two key areas: basic shapes and geometric concepts, and understanding dimensions and scaling.
Basic Shapes and Geometric Concepts
At the very heart of 3D modeling are basic shapes. Think about it: every complex model is essentially a combination of simple geometric forms. These forms include cubes, spheres, cylinders, and pyramids. Knowing how these shapes interact with each other and understanding their properties is essential.
- Cubes can serve as the starting block for many designs. They're often used in architecture and product design because they represent stability.
- Spheres provide uniformity and balance, frequently utilized in organic shapes like characters or nature-inspired designs.
- Cylinders are invaluable for creating objects with curves, like bottles or barrels.
- Pyramids, though less commonly employed, can still add a unique twist to your creations, especially in structures like roofs.
When working with these shapes, it's crucial to consider aspects like edges, vertices, and faces. The interplay generates visual interest and can affect the model's final look in print. Moreover, more complex structures can often be built by combining these basic forms. But don’t forget, while simple shapes are foundational, they are not always straightforward to work with; the subtleties in proportions can make a big difference.
"If you can’t explain it simply, you don’t understand it well enough." - Albert Einstein
Being comfortable with geometric concepts enables you to experiment creatively and helps streamline the modeling process. This familiarity means less hassle downstream when preparing your model for printing.
Understanding Dimensions and Scaling
Next comes the need to comprehend dimensions and scaling—two sides of the same coin. While basic shapes bring your designs to life, dimensions dictate how those shapes occupy space. Misjudging these can lead to disastrous results, particularly in 3D printing where precision is king.
- Dimensions involve measurements of length, width, and height. Each dimension directly impacts the volume of your model. Recognizing this helps you optimize designs for specific applications—whether it's crafting components for machinery or sculptures.
- Scaling plays a vital role, especially when transitioning from concept to a tangible object. Not everything can, or should, be created at full size. Learning how to scale a design accurately allows for flexibility in production. It enables you to create miniatures or massive structures, depending on your needs.
Being mindful of dimensions and scaling is necessary not only for aesthetics but also for ensuring the practicality of your prints. Structures that are too large might not fit in the printer, while those that are too small can lose essential details in the print. Knowing how to manipulate sizes effectively can save you from recurrent pitfalls.
Sketching Your Initial Design
Sketching serves as the cornerstone for creating a successful 3D model. Before diving into complex modeling software, doing a simple sketch can drastically streamline the entire process. It allows for creative freedom while still being structured enough to guide the final output. By taking time to visualize ideas on paper, designers solidify concepts, minimize guesswork, and translate abstract thoughts into tangible forms.
A detailed sketch can minimize oversights that might crop up in later stages of development. Not only does it serve as a navigational tool through the vast sea of 3D design, but it also facilitates communication, especially in collaborative projects. Sharing a sketch can often speak volumes compared to verbal descriptions alone. Ultimately, sketching lays the groundwork that can make or break the modeling process.
Using 2D Sketches as a Reference
Utilizing 2D sketches as a reference in 3D modeling is akin to having a map before a journey. These references prevent aimless wandering during the design phase. By translating a sketch into a digital format, the designer maintains the original vision while benefiting from the flexibility and precision of modern modeling tools.
When designing a model using sketches:
- Clear Outline: A well-defined sketch helps to create a clear outline of dimensions, shapes, and overall structure that can then be adapted in 3D software.
- Perspective and Proportions: Early sketches can highlight any perspective peculiarities or proportion inconsistencies before they become problematic in 3D space.
- Functional Elements: Sketching can aid in identifying functional elements such as joints, openings, or features critical to the model's utility.
A productive way to approach this is to trace over the 2D sketches in the modeling software, using them as a foundation to build upon. This approach captures both the aesthetic and functional aspects, ensuring fidelity to the initial idea.
Tips for Effective Sketching
While sketching might seem straightforward, some tips can enhance the efficacy of this process:
- Use the Right Tools: Pencils, markers, and even digital tablets; the choice of tools can impact how well ideas are communicated. Each tool offers different textures and depths.
- Think in Layers: Decomposing elements into layers (e.g., foreground, midground, background) can clarify complex designs and help your viewer understand the model’s dimensions.
- Focus on Functionality: Sometimes, it’s easy to get caught up in aesthetics. Ensure that the functionality is at the fore, as too many embellishments can obfuscate the core purpose of the model.
- Iterate and Evolve: Don't hesitate to sketch several versions of an idea. Each iteration brings new insights or improvements that may not have been apparent on the first go.
Sketching is not merely the starting point; it can continue to be a reference throughout the modeling process. By weaving these simple practices into your routine, you not only enhance your design but also enrich the final product.
"A good design starts with a great sketch. It’s the silent dialogue between idea and form, where each mark carries the weight of potential."
Understanding the importance of sketching and honing your skills in creating effective sketches lays a strong foundation for subsequent phases in 3D modeling. Embracing this practice ensures that the journey from concept to completed model is as smooth as possible, with minimal bumps along the way.
Core Principles of 3D Modeling
When diving into the world of 3D modeling, understanding the core principles is akin to laying a solid foundation before erecting a skyscraper. It’s not just about knowing how to twist and turn shapes; it’s about grasping the very language of the digital space you’re navigating. This section emphasizes the essential elements, benefits, and considerations of the core principles of 3D modeling that resonate with both novices and experts.
Polygons, NURBS, and Meshes
Within the realm of 3D modeling, the conversation often begins with polygons, NURBS, and meshes—three distinct yet interrelated structures that form the fabric of digital designs.
- Polygons are the simplest form of 3D shapes, typically composed of flat surfaces with straight edges. They are the building blocks of 3D models. Most notably, triangles and quadrilaterals are the most common types.
- NURBS, which stands for Non-Uniform Rational B-Splines, provides more flexibility than basic polygons. They allow for smooth curves and complex surfaces, making them invaluable in modeling intricate designs, such as automotive bodies or organic shapes.
- Meshes blend both concepts, comprising a collection of interconnected polygons. This approach here enables the representation of more complex surfaces and forms than what a single polygon could offer.
Understanding when to harness each of these structures can significantly affect your model’s aesthetic appeal and functionality. For instance, a car designer may favor NURBS for its smooth curves, while a game developer could lean towards polygons for their simplicity and compatibility with various engines.
"Selecting the right modeling approach isn’t just a matter of comfort—it's fundamentally tied to the requirements of the project and the final output you aim to achieve."
Creating Complex Structures
Crafting complex structures in 3D modeling does not merely involve slapping polygons together; it's a delicate dance of technique, creativity, and precision. Here lies an array of strategies that can make or break a model's integrity.
- Layering Techniques: One effective method to develop intricate designs is layering; you can build complexity gradually. This allows for better control over each segment of your structure, as modifications can be made without reworking the entire model.
- Boolean Operations: These operations combine or subtract one shape from another. Imagine taking two blocks and merging them or carving one from another. This is essential for creating openings or unique features without manually adjusting every vertex.
- Subdivision Surfaces: When aiming for smoother results, subdivision surfaces refine the model by increasing resolution in specific areas. This is particularly advantageous when detail is required around edges or curvatures, allowing the model to retain its overall shape while enhancing its finesse.
- Modifiers and Sculpting Tools: Most modern software includes modifiers that alter geometry dynamically. Sculpting tools further enhance this by giving you freeform control over the model’s surface, akin to molding clay.
The complexities of 3D modeling require patience and practice. However, when you harness these techniques effectively, you’ll find that your capacity to create detailed and realistic models expands significantly. Ultimately, developing complex structures is not just about technical input, but also about fostering an imaginative approach to 3D design.
Optimizing Your Model for 3D Printing
Optimizing your model for 3D printing is a crucial step that can mean the difference between a successful prototype and a tangible disappointment. The optimization process encompasses a range of considerations that enhance not only the visual appeal of your design but also its structural integrity and feasibility during the printing phase. Proper optimization steps lead to fewer failures, reduced material waste, and ultimately save time—valuable commodities in any project.
Checking Wall Thickness and Infill
First and foremost, wall thickness is closely tied to the durability of the printed object. It's not just about looking good; if the walls are too thin, the model might collapse during printing or fall apart upon first use. As a guideline, a minimum wall thickness of at least 1mm is generally advisable for most materials, although some filaments allow for thinner variations. By fine-tuning this aspect, individuals can reinforce their designs, especially for functional parts like gears or brackets, ensuring they hold up under stress.
Infill percentage directly influences weight, strength, and material usage. Here are some points to consider when determining your model's infill settings:
- Functional Items: For objects that need to withstand forces, like tools or fixtures, a higher infill of around 50% or more enhances sturdiness.
- Aesthetic Models: For decorative pieces where appearance trumps utility, a lighter infill of 10-20% is usually sufficient. It looks good and saves on material.
- Testing: Getting the perfect balance often involves trial and error. Running a few test prints can help nail down the right balance for specific projects without overspending on materials.
"A stitch in time saves nine." The same applies to wall thickness and infill. Spend time optimally designing now to prevent headaches later!
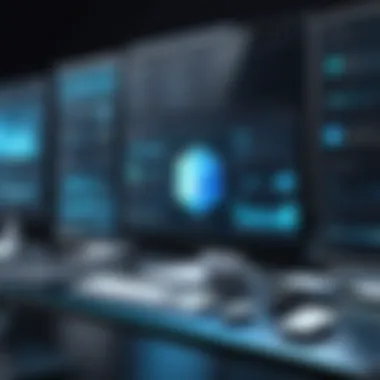
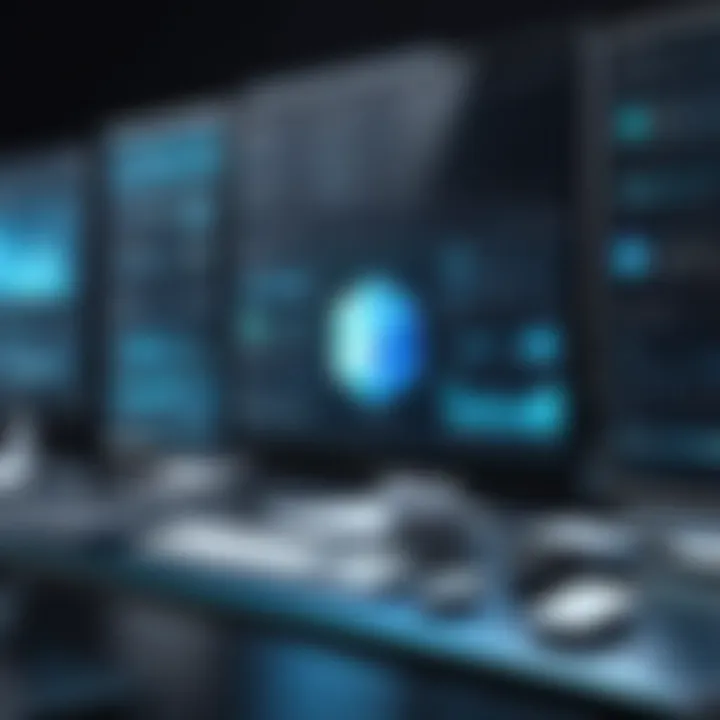
Minimizing Overhangs and Supports
Next on the list is dealing with overhangs and supports. They are often the nemeses of 3D printing. When a model has features that extend outward without sufficient support beneath, it can lead to print failures or unsightly artifacts on the surface. To avoid the headache of clearing excess support material later, it’s wise to design with overhang considerations from the get-go.
- Angles: A common rule of thumb is to keep overhang angles under 45 degrees. If your design includes steeper overhangs, they may need additional support.
- Built In Supports: Some modeling software allows you to add supports directly to the design. Consider strategically placing them so they can be easily removed without damaging the final product.
- Alternative Strategies: Another approach is to design models in such a way that they can be printed on their side or even with a different orientation, minimizing the need for supports. This can give surface quality higher appeal and reduce material costs.
Essentially, an eye for detail in this phase can help with the end result. The better one gets at anticipating and mitigating potential issues, the more fluid the printing process becomes.
Exporting Your Model
The act of exporting your 3D model is more than just a mere final step. It's a critical juncture that can significantly influence how your model is perceived and utilized after it's crafted. At this stage, the model should be in its best shape, ready to transition from a digital blueprint to a tangible product. Ignoring the subtleties of this phase can lead to unexpected pitfalls down the line. Therefore, understanding the specifics involved in exporting is paramount.
When you take the time to consider factors like file formats and compatibility, you essentially open up avenues for smoother integration into different printing processes. A well-exported model can also save you from reworking issues that could arise during or after the printing phase.
File Formats and Compatibility
When exporting your model, grasping the various file formats available is essential. Different 3D printing technologies often require specific file types. Here are a few common formats you may encounter:
- STL (Stereolithography): One of the most widely used formats in the 3D printing community. It's simple and effective, capturing geometry without color or texture details.
- OBJ: Similar to STL but can hold texture and color information, making it more versatile for aesthetically complex models.
- FBX: Primarily used in animation and media; it's less common in 3D printing but still an option for certain workflows.
- AMF (Additive Manufacturing File): A newer format that supports multiple materials and colors, though it's not universally adopted yet.
Knowing which format your printer supports ensures seamless communication between the software and the hardware, minimizing headaches later on. Always check the printer’s documentation to steer clear of any compatibility issues.
Preparing for Slicing Software
Once the model is exported in the correct format, the next step is prepping for slicing software. Slicing software acts as the middleman, converting your 3D model into a format that a 3D printer understands. This process involves dividing the model into layers and defining specifics like print speed, layer height, and infill density.
Here are a few considerations for smooth sailing:
- Review Exported Model: Before diving into slicing, recheck your exported file. A quick look can save you from unpleasant surprises.
- Import Properly: Different slicing software can behave oddly with certain formats. Make sure to follow any prompts that the software offers to correct or optimize imported files.
- Adjust Settings: Once imported, take a moment to tweak the settings. If your model has intricate designs, you might want to adjust the layer height to achieve finer details.
In essence, exporting your model effectively and preparing it for slicing software isn't just busy work; it's a pivotal step that can dictate the quality of your final printed piece. Each detail plays a role in ensuring that the final output resonates with the quality you envisioned.
Using Slicing Software
In the realm of 3D printing, the journey from a virtual model to a physical object is a multi-step process. One of the most critical stages in this journey is the use of slicing software. This software acts as the bridge that transforms your 3D models into instructions that a printer can understand. Without slicing, even the most meticulously designed model would be rendered useless in the hands of a printer.
Overview of Slicing Software
Slicing software is fundamentally designed to analyze a 3D model, break it down into thin horizontal layers, and generate a comprehensive set of instructions, commonly in G-code language, for the 3D printer. This process, termed "slicing," ensures that the printer knows exactly how to construct your model layer by layer.
There are numerous slicing software options out there each with its unique feature set. Some of the most popular ones include Ultimaker Cura, PrusaSlicer, and Simplify3D. These programs are pivotal in ensuring your final print accurately reflects your digital design.
When choosing slicing software, consider the following:
- User Interface: An intuitive interface can save you time learning the software's ins and outs.
- Customization Options: Different materials and models may require specific settings. A good slicer offers adjustable parameters such as layer height, infill, and print speed.
- Support for Materials: Verify that the software handles the type of materials you plan to use.
- Integration: Some better slicers work well with various CAD tools smoothly, which can save you time in exporting and importing files.
Importing and Adjusting Your Model
Once you've chosen your slicing software, the next step is importing your 3D model. Generally, these programs support common file formats like STL or OBJ, which makes it easier to import your design.
- Importing Process: Typically, you'll use the "Import" option found in the software menu. Just navigate to your model file, select it, and your 3D design will appear on the workspace. From here, you'll have the ability to adjust its position, scale, and orientation.
- Adjustments: It’s important to ensure that your model is properly oriented for printing. You may want to rotate your model, so it prints flat on the bed or rises without support. This can significantly affect the quality of the final print. For instance, models with heavy overhangs should generally be positioned to minimize this to avoid printing failures.
- Sizing and Scaling: Maybe your design fits on paper perfectly, but in practice, it should fit the actual build plate of your printer. Use the scaling tools sparingly; scaling can distort your design if not handled correctly.
In summary, slicing software is an integral part of 3D printing that can’t be overlooked. Mastery in using it not only simplifies the workflow but also enhances the quality of the end product. By understanding how to effectively import and adjust your models, you're setting the stage for better prints and less frustration.
Choosing the Right Materials for 3D Printing
Selecting the right materials for 3D printing is a cornerstone of the entire process. Each material offers different properties, which can vastly change the outcome of the printed model. A well-chosen material doesn’t just enhance the performance of the model but can also ensure its durability and aesthetic appeal. There's a myriad of options available today, and understanding these can be the difference between a successful print and a costly failure.
Different applications demand different material characteristics. For instance, if you're crafting a model intended for functional use, you might prioritize strength and flexibility, whereas an artistic design may demand vibrant colors and surface finish. Ultimately, knowing the ins and outs of materials available is crucial for any designer looking to navigate dynamic printing environments.
Common Materials and Their Properties
When you step into the world of 3D printing, you quickly realize that the material is king. Here's a look at some common materials:
- PLA (Polylactic Acid):
A biodegradable plastic made from renewable resources. As a favorite among beginners, PLA is easy to print with and offers excellent detail. Its rigidity makes it ideal for decorative items but less suited for functional parts that undergo stress. - ABS (Acrylonitrile Butadiene Styrene):
A strong plastic that withstands heat better than PLA. It’s commonly used for functional prototypes. However, printing with ABS can be tricky due to warping issues. - PETG (Polyethylene Terephthalate Glycol):
This material is excellent for combining the best of PLA and ABS. It provides durability and ease of printing while being resistant to moisture. It's often used for parts requiring better mechanical properties. - Nylon:
Known for its strength and resilience, nylon is used in applications where flexibility and endurance are required. It can be a bit tricky to print due to its tendency to absorb moisture, but it’s a solid choice for functional items. - TPU (Thermoplastic Polyurethane):
A flexible material, great for creating soft objects like phone cases or wearables. TPU may take longer to print and requires careful settings to achieve the desired results.
Material Considerations Based on Application
Choosing the right material is only half the battle; the application truly dictates what should be used. Here are some tidbits to keep in mind:
- Prototyping:
For rapid prototypes or concepts, PLA is often the go-to. It allows for quick iterations while still capturing fine details. - Functional Parts:
Think about using durable materials like ABS or PETG for pieces that need to withstand functional demands. Components in mechanical assemblies should be robust and stable under pressure. - Aesthetic Models:
When appearance matters, consider materials that offer a range of colors and finishes. PLA shines here, along with specialized filaments that provide a shiny or silk-like finish. - Medical Applications:
Biocompatible filaments, like certain grades of PLA, are critical in medical applications. Knowing the regulatory standards for these applications is vital. - Engineering Models:
For engineering simulations, look to use nylon or composite materials that can better represent real-world stresses and loads.
"The material you choose can dictate not only the functionality of a print but also how it holds up over time and under different conditions. Understanding these properties allows designers to tailor their creations to specific needs."
In summary, diving into materials requires more than mere preference—it's about matching the materials with the intended application. Understanding these nuances not only helps in making informed decisions but also sets the stage for exploring the full breadth of what 3D printing has to offer.
The Printing Process
The printing process stands as a pivotal segment in the journey from a digital model to a tangible object, encapsulating the heart of 3D printing technology. Understanding this process is essential, not only for ensuring the successful output of the designs created but also for troubleshooting potential hiccups along the way. By grasping the mechanics at play, practitioners can optimize their efforts, yielding better results.
3D printing is often likened to cooking; without the right ingredients and precise timing, you might end up with a half-baked dish—or in this case, a flawed print. The importance of this stage cannot be overstated as it lays the groundwork for the model's fidelity and accuracy during the final output.
Setting up the 3D Printer
Setting up the 3D printer is akin to tuning an instrument before a concert. Every setting needs to be just right to ensure a flawless performance. An effective setup includes several critical considerations:
- Printer Calibration: Calibrating the printer is a vital initial step. This step involves adjusting the bed level to ensure the nozzle maintains the proper distance from the build platform. Without correct calibration, the first layers can fail, leading to complications down the line.
- Material Loading: Load the filament or resin properly based on the 3D printing technology being employed. For filament-based printing, ensuring that the material feeds smoothly from the spool to the extruder is crucial. Meanwhile, resin printers require precise handling to maintain cleanliness and ensure smooth operation.
- Configuring Settings: Before hitting the "print" button, one must delve into the printer settings as per the project’s requirements. This includes adjusting temperature, speed, and layer height, ensuring they align with the filament’s specifications. Overlooking these settings might culminate in wasted resources.
To help keep the process aligned, consider using a checklist during setup. Such a list might include:
- Calibrate the bed height.
- Check filament feed rate.
- Confirm temperature settings.
- Review slicing settings for compatibility.
"A well-prepared printer is half the battle won when creating a flawless model."
Monitoring the Print Job
Monitoring the print job reveals itself as one of the more dynamic aspects of the printing process. It is certainly worth your attention, as numerous factors can influence the outcome of a print in real-time.
As the printer hums along, here are key areas to keep an eye on:
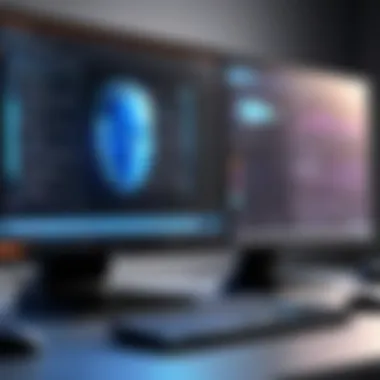
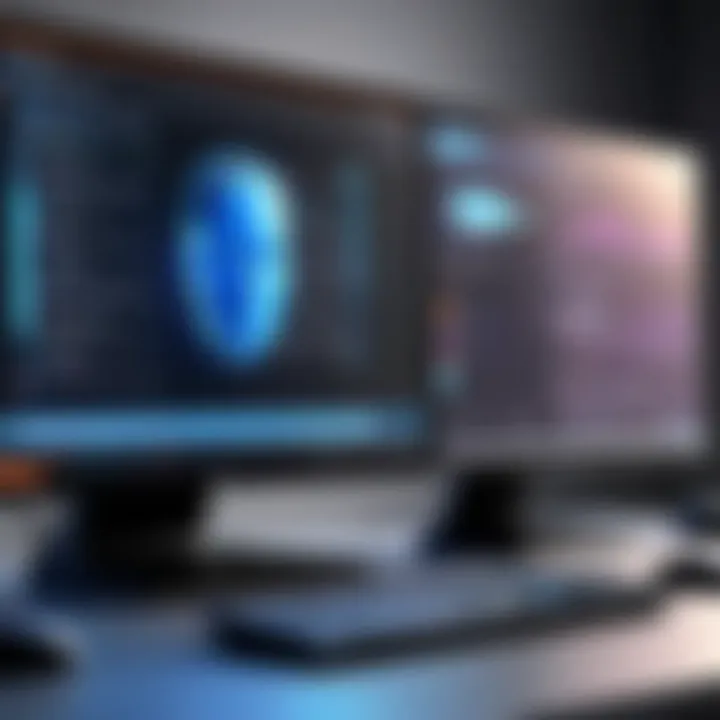
- Watch for Layer Adhesion: Ensuring good adhesion between layers can make or break the print. If layers don’t bond correctly, the structure lacks strength and integrity. Using your intuition to check for any gaps or separations as the print progresses can save you time and material.
- Pay Attention to Extrusion: If the extruder starts skipping, which can manifest as uneven or disappearing lines, it may suggest clogs or inadequate material feeding. Timely intervention can rescue the print from imminent failure.
- Thermal Stability: Monitoring the temperature can help prevent warping or other heat-related issues that can occur during higher printing temperatures. Ambient conditions, such as drafts or excessive heat, can also affect print quality and should be controlled.
To streamline the monitoring process, consider employing a separate camera system that allows remote viewing. This way, you can manage multiple jobs and even engage in other tasks while still keeping an eye on the crucial aspects of your printing job.
All things considered, the printing process is not merely a mechanical function. It is a series of intricate and interrelated actions that demand attention and care. With a thorough understanding of these, the chances of achieving a successful print greatly increase.
Post-Processing Your Printed Model
Post-processing holds a significant place in the realm of 3D printing. After the printer has completed its work, the real artistry often begins. This phase not only enhances the aesthetic appeal of your model but also its functional integrity. Whether it’s to improve surface finish or prepare the object for its intended application, post-processing helps in creating tangible results that can elevate a simple print to an impressive end product.
The importance of this stage lies in resolving the imperfections that might arise during the printing process. Consider this: even the best 3D printer can leave behind artifacts, layer lines, or support marks that detract from the overall quality of an object. By carefully addressing these issues, one can refine a model into something that truly meets professional standards.
Removing Supports and Finishing Edges
One of the first tasks in post-processing is to remove any supports used during printing. Supports are essential for overhanging sections, but they can leave behind unsightly remnants. These won’t just be visible; they can affect the model's functionality.
When removing supports, it is prudent to proceed with caution. It helps to use tools like pliers or hobby knives, making sure to work gently to avoid damaging the underlying model. After supports are removed, you often find rough edges or uneven surfaces. These can be smoothed out using sanding techniques or more advanced methods such as grinding with a Dremel tool.
"Careful attention to detail in post-processing can mean the difference between a good model and a great one."
Painting and Surface Treatments
After the supports are gone and edges are refined, the true magic of post-processing comes into play with painting and surface treatments. Here, the goal stretches beyond mere appearance; it ties in closely with the functionality and durability of the printed model.
If you're aiming for a polished look, priming the surface is essential. This prevents the paint from soaking into the material, allowing for a smoother finish. Choosing the right type of paint is also crucial. Acrylic paints often provide a suitable and adaptable medium for varied materials while ensuring a vibrant finish. For models designed to endure wear, consider using specialized coatings or sealing agents. These treatments not only enhance the model's appearance but also extend its lifespan.
Incorporating textures or patterns through techniques such as hydro dipping can also add a personalized flair to a model. This is especially relevant for businesses looking to create distinct branding elements through custom 3D prints.
Through diligent post-processing, your model can transit from a rough draft to a polished sculpture, ready for its practical application or presentation. This step is not merely a luxury; it’s an essential process that contributes significantly to the effectiveness and appeal of a 3D printed object.
Common Issues and Their Solutions
In the realm of 3D printing, encountering problems is as common as breathing; however, each hiccup presents an opportunity for learning and improvement. Understanding the various common issues that can arise during the 3D modeling and printing process is essential not just for troubleshooting, but for enhancing the final product’s quality. Addressing these issues comprehensively ensures that creators can avoid costly mistakes and get more familiar with the intricate relationship between design, material, and printer technology.
Print Failures and Remedies
Print failures can be particularly frustrating, especially after investing considerable time and resources into the modeling and printing process. Tiny errors can derail an entire project, leading to wasted materials and potential delays. Here are some common print failures along with remedies:
- Layer Separation: When layers don’t stick together, it might lead to a weak structure. Ensuring the right temperature settings for both the nozzle and the bed can help maintain the adhesion needed.
- Stringing: This occurs when thin strands of plastic form between parts of the model during printing. Reducing the printing temperature and increasing travel speed can significantly address this.
- Warping: As the model cools, it may contract unevenly, resulting in warping. Choosing the right bed adhesive or using enclosures to maintain heat can preserve the shape.
- Under-extrusion: This results in gaps in the model. Regularly checking the filament path for blockages and adjusting the extrusion multiplier can help avoid this.
Sometimes, it’s necessary to go back to the drawing board. Pay close attention to the printer's settings and adjust accordingly. As they say, "measure twice, cut once."
Model Errors to Avoid
Creating a 3D model is not just about aesthetics or following a vision; it’s crucial to develop a model that’s ready for printing. Here are errors to sidestep:
- Inadequate Wall Thickness: Failing to ensure proper wall thickness can lead to brittle prints. Always check the specifications for your material to determine the minimum and optimal wall thickness.
- Complex Detail: While intricate details may look impressive, over-complicating a design can overwhelm the printing process. Simplifying complex features often yields better results.
- Non-Manifold Edges: This issue arises when edges don’t connect properly, making it impossible to create a solid model. Regularly use validation tools within your software to detect such problems before exporting.
- Incorrect Scaling: Sometimes, a miscalculation in the dimensions can throw off the entire project. Always verify the scaling parameters when transitioning from modeling to printing.
By recognizing and addressing these issues beforehand, one can streamline the workflow significantly.
"An ounce of prevention is worth a pound of cure."
In the end, the key to successfully navigating the common pitfalls of 3D modeling and printing lies in a combination of foresight and practical troubleshooting skills. Constantly evaluate your processes and adopt best practices where possible.
Advances in 3D Modeling Software
The world of 3D modeling has been continually evolving, with innovations that can make a significant difference in efficiency, creativity, and ultimately, the quality of printed objects. Understanding advances in 3D modeling software is crucial not only because it influences how designs are created, but also because these advancements directly impact the ease of translating complex ideas into workable models ready for 3D printing.
Emerging Technologies in 3D Design
Recent developments in 3D modeling software often stem from breakthroughs in technology that enhance user experience and output quality. Technologies like Machine Learning and Artificial Intelligence have been making waves in the field. Imagine software that learns from previous designs, suggesting enhancements or troubleshooting potential issues before they arise. This kind of integration helps users navigate the modeling landscape more effectively, whether they are novices or seasoned professionals.
Additionally, cloud computing has transformed how collaboration occurs in 3D design. Designers, engineers, and artists can work on the same project simultaneously from different locations, facilitating clearer communication and faster iterations. Tools such as Autodesk Fusion 360 and Onshape allow multiple users to view and edit designs in real-time, bridge any gaps in expertise by allowing knowledge sharing within a team, and encourage stronger bonding through collaborative projects.
Moreover, the growing use of virtual and augmented reality in modeling is another game changer. These technologies allow users to visualize their design in three-dimensional space before finalizing it. This immersive experience can significantly reduce errors in scaling and dimensions long before the first print is attempted. As a designer puts on a pair of VR goggles, they can almost 'walk around' their model, spotting potential issues that might not be evident on a standard screen.
Future Trends in 3D Printing and Modeling
Looking towards the horizon, several trends are shaping the future of both 3D printing and modeling. One of the major trends is the increased focus on sustainability. As environmental concerns grow, there’s a push towards using biodegradable materials and designing with recyclability in mind. New software tools are emerging to help designers consider the life cycle of their products right from the modeling stage. This means creating designs not just for functionality, but for eco-friendliness as well.
Additionally, advancements in generative design are expected to gain traction. Not only does this approach allow software to propose multiple design alternatives based on specified requirements, but it also fosters innovation in creating lightweight forms with maximum strength. For instance, using algorithms, the software can explore thousands of combinations to find the most efficient layout of materials, which can revolutionize how we think about product functionality.
Also, as consumer needs become increasingly specific, customization options in 3D modeling software will also expand. Users will push for more intuitive interfaces that let them tailor designs more easily, without requiring extensive training in CAD software. Companies might offer templates based on popular products, enabling everyday users to modify designs to better fit their personal needs.
Advances in 3D modeling software don't just change the practicalities of designing; they transform the very fabric of creativity, merging technology with artistry in ways we are just beginning to explore.
Ending
The progress in 3D modeling software not only simplifies the design process but also opens up new avenues for unique creations. As both technology and user demands progress, the ability to create tailored models will continue to evolve, pushing the boundaries of what’s possible in both 3D printing and modeling. Companies and individuals who stay on top of these trends will be best positioned to create innovative products that resonate with modern needs.
The End and Final Thoughts
As we wrap up this extensive guide on creating 3D models for 3D printing, it's essential to reflect on the key elements we've explored. The journey from concept to a physical object not only demands technical skills but also a creative mindset. Each stage, from selecting the right software to optimizing designs for print, plays a crucial role in ensuring the final model meets expectations, both functionally and aesthetically.
Understanding the 3D modeling process lays a solid groundwork for any individual or organization venturing into 3D printing. With a comprehensive grasp of the principles, you can avoid common pitfalls and significantly enhance the quality of your prints. Remember, the essence of your digital creation is a culmination of various factors, ranging from wall thickness to the compatibility of file formats.
Moreover, the discussion on advances in 3D modeling and future trends paints a promising picture for this technology. The landscape is shifting rapidly, with emerging tools and processes making modeling more accessible and efficient. Keeping abreast of these innovations ensures that you, as a creator, remain relevant and competitive in this dynamic field.
"The secret of getting ahead is getting started." - Mark Twain
Continuing to explore and adopt innovative methods can keep your skills sharp and your designs at the forefront of technology. Embrace the learning journey, whether through workshops, online resources, or community engagements.
Recapping the 3D Modeling Process
Let’s summarize the fundamental steps you've encountered:
- Understanding the Basics: Familiarize yourself with 3D modeling concepts, including shapes, dimensions, and scaling, to achieve a robust foundation.
- Software Selection: Choose the right modeling software that aligns with your project’s requirements—be it free tools or paid solutions.
- Sketching: Use 2D sketches as blueprints to guide your 3D design process. This visual approach simplifies transitions from flat drawings to volumetric forms.
- Model Creation and Optimization: Pay heed to wall thickness, overhangs, and other elements crucial for print success.
- Exporting and Preparing: Selecting the right file format is key for compatibility with slicing software.
- Using Slicing Software: Adjust your model parameters before printing to maximize final output quality.
- Post-Processing: A careful finish can elevate your printed model, bringing it closer to your original vision.
Each of these stages contributes to the overall effectiveness of your modeling efforts, guiding you towards tangible results in your 3D projects.
Encouragement for Continuous Learning and Experimentation
In a field as dynamic as 3D modeling, stagnation is your enemy. Experimentation is the lifeblood that nourishes creativity and innovation. It’s vital to foster a mindset that embraces trial and error. For instance, try different materials or adjust settings on your printer, even if the results don't meet your expectations at first. Each attempt provides valuable insights that sharpen your skills.
Participating in forums or discussion platforms like Reddit can also be immensely beneficial. Engaging with a community of like-minded individuals can offer new perspectives and techniques that you might not encounter on your own. Furthermore, as you grow more comfortable with your tools, don’t hesitate to outreach for feedback on your projects. Active participation and peer review can dramatically boost your learning curve.
Take advantage of resources available on Wikipedia and Britannica; they can serve as excellent reference points for both basic concepts and advanced techniques. Remember, learning is a continuous process, and in the fast-paced world of technology, adaptability is paramount. So, tap into that curiosity, keep pushing boundaries, and watch your capabilities flourish.