Navigating Industry 4.0 with Manufacturing Execution Systems
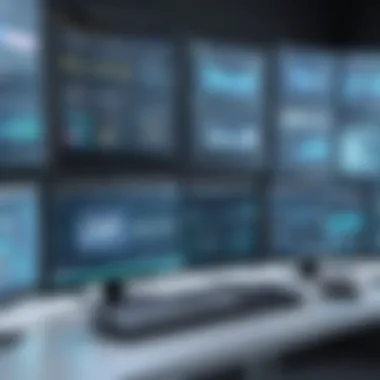
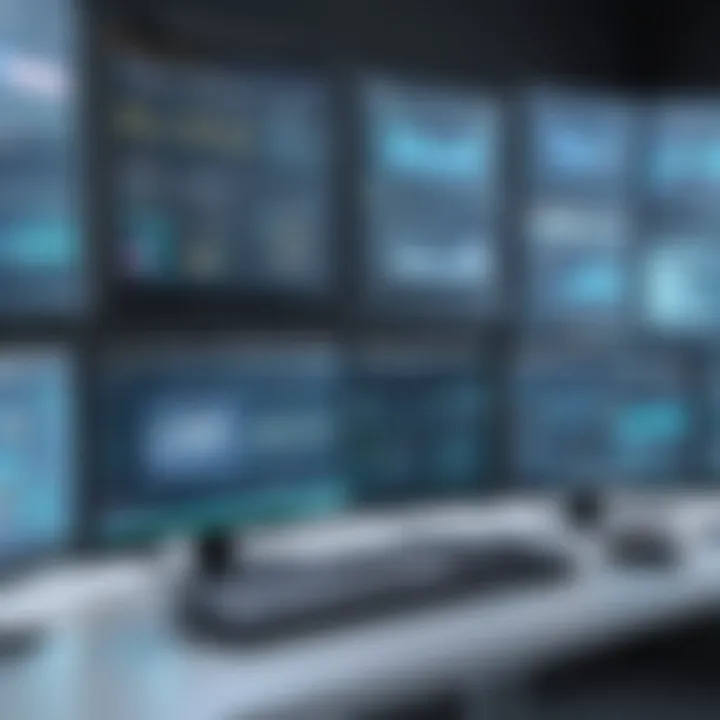
Intro
The advent of Industry 4.0 marks a pivotal evolution in manufacturing processes. Central to this transformation are Manufacturing Execution Systems (MES), which serve as critical tools to enhance production efficiency and data management. This article aims to navigate through the depth of MES, shedding light on their functionalities, impact on operational excellence, and the challenges faced during implementation. Also, future trends concerning MES in the Industry 4.0 landscape will be examined.
Brief Description
Manufacturing Execution Systems are sophisticated software solutions designed to monitor and manage manufacturing operations in real time. They serve as a vital link between the enterprise resource planning systems and the manufacturing floor. Through the integration of MES, companies can streamline their production processes, ensure quality control, and improve overall operational visibility.
Overview of the software
MES provides a real-time view of production processes, allowing manufacturers to keep track of the shop floor activities. This ensures that production schedules are adhered to, materials are correctly accounted for, and equipment is optimally utilized. With the integration of Internet of Things (IoT) capabilities, MES can gather data from various sensors and devices giving rise to enhanced decision-making capabilities.
Key features and functionalities
Some key features of MES include:
- Production Tracking: MES continuously monitors production processes, providing updates on the status of work in progress.
- Quality Management: The system allows for real-time quality data collection and analysis, helping to identify defects early in the production cycle.
- Data Analysis: MES processes vast amounts of data to derive insights that can help in optimizing production.
- Resource Management: MES ensures that machinery and human resources are utilized effectively, reducing downtime and wastage.
"The real-time capabilities of MES enable quicker responses to production issues, fostering a culture of continuous improvement."
System Requirements
When considering the implementation of an MES solution, it is essential to align with the necessary system requirements. This ensures that the software can operate efficiently within the existing infrastructure.
Hardware requirements
Typical hardware requirements for an MES include:
- Servers: Depending on the scale of operation, a robust server setup may be needed to handle the software and store data.
- Network Infrastructure: A reliable network is crucial for seamless data transfer between machines and the MES.
- User Devices: Computers, tablets, or mobile devices for operators and management to access the MES.
Software compatibility
Furthermore, the MES must be compatible with existing manufacturing software, such as ERP systems like SAP or Oracle. Compatibility ensures that data flows smoothly between different systems, which is critical for effective production management.
Understanding Industry 4.
The concept of Industry 4.0 is crucial for modern manufacturing. It represents the fourth industrial revolution, characterized by the integration of digital technologies into manufacturing processes. This transformation changes how products are designed, manufactured, and delivered. Understanding Industry 4.0 involves grasping its core elements, including connectivity, automation, and data exchange.
Definition and Origins
Industry 4.0 originated in Germany, where it was first introduced during the Hannover Fair in 2011. This initiative aimed to enhance the competitiveness of manufacturing through intelligent networks. Simply put, Industry 4.0 integrates physical production with digital technology, emphasizing efficiency and flexibility. It relies on interconnected systems that communicate with each other to optimize production processes. This integration leads to smarter factories that leverage real-time data for decision-making.
Key Technologies Driving Industry 4.
The framework of Industry 4.0 is underpinned by several key technologies that foster innovation and efficiency.
Internet of Things
The Internet of Things (IoT) connects machines, sensors, and devices to the internet. This connectivity allows for seamless communication between different components of the manufacturing process. A key characteristic of IoT is its ability to collect and analyze data from multiple sources in real-time. This capability enables manufacturers to monitor performance, predict maintenance needs, and improve overall operational efficiency. Its unique feature includes big data utilization, allowing informed decisions based on actionable insights. However, IoT requires robust cybersecurity measures to protect sensitive data.
Artificial Intelligence
Artificial Intelligence (AI) significantly enhances manufacturing by analyzing data and making predictions. AI's key characteristic is its ability to learn from data, identifying patterns that humans might overlook. This capability offers manufacturers the ability to optimize production schedules and enhance quality control. One unique feature of AI is its capacity for predictive maintenance, reducing downtime and saving costs. Yet, implementing AI can be challenging due to data privacy concerns and the need for substantial investment.
Cloud Computing
Cloud Computing allows manufacturers to store and access data over the internet. This technology is beneficial because it facilitates data sharing across different locations and systems. A distinctive aspect of cloud computing is its scalability, enabling companies to adjust resources as needed. The advantages include cost savings and flexibility, but potential disadvantages involve reliability and data security issues.
Big Data Analytics
Big Data Analytics refers to the process of analyzing large datasets to uncover trends and insights. This technology plays a vital role in making informed decisions within manufacturing. Its key characteristic is the ability to process vast amounts of data quickly. It enhances operational efficiency and supports predictive analysis, enabling better resource allocation. However, managing and interpreting large datasets can be a complex task requiring specialized skills.
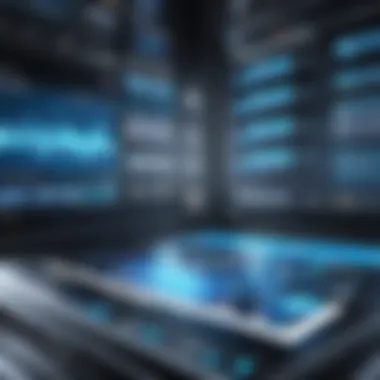
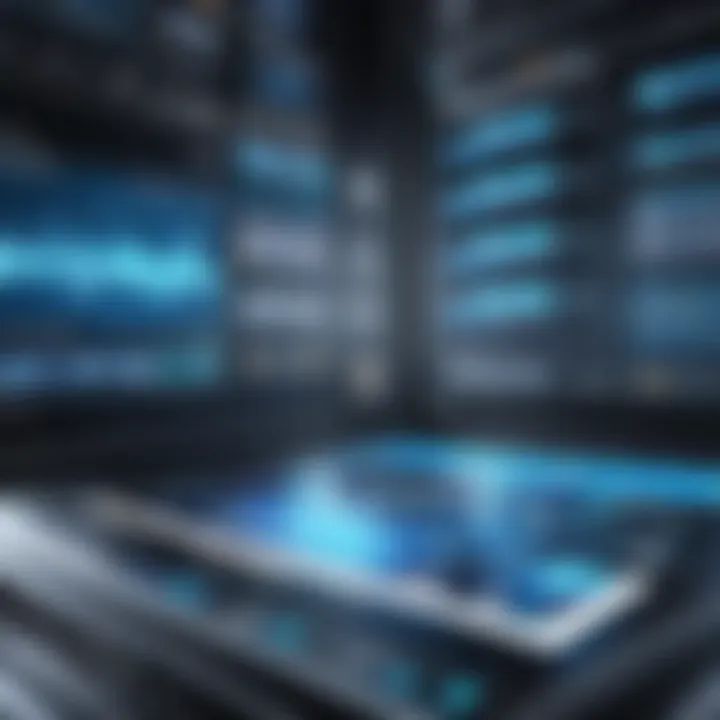
Benefits and Opportunities
Understanding the benefits of Industry 4.0 reveals numerous opportunities for manufacturers.
Increased Efficiency
Increased efficiency translates to reduced production time and lower costs. The integration of advanced technologies automates routine tasks, allowing employees to focus on more strategic activities. A significant characteristic of increased efficiency is the optimization of resource utilization. The unique feature of this benefit is its direct impact on productivity. While the initial investment might be high, the long-term gains in efficiency and profitability often outweigh costs.
Enhanced Customization
Enhanced customization allows manufacturers to create products tailored to customer needs. This opportunity is crucial in today's market, where consumers expect personalization. A key characteristic of this trend is flexibility in production processes. Manufacturers can quickly adjust their operations to accommodate changing demands. However, too much customization can complicate supply chains and increase production challenges.
Improved Supply Chain Management
Improving supply chain management is another advantage of Industry 4.0. Utilizing data analytics provides better visibility and control over the supply chain. A notable characteristic is real-time tracking of goods and resources, which enhances overall coordination. This improvement leads to reduced delays and better inventory management. However, integrating new technologies into existing systems can be complex and may require significant changes to established processes.
What are Manufacturing Execution Systems?
Manufacturing Execution Systems (MES) are critical components in the landscape of modern manufacturing. They serve as a bridge between higher-level enterprise resources and the factory floor, managing and monitoring work in progress. By gathering real-time information, they help manufacturers enhance their processes, increase efficiency, and improve quality control. In the context of Industry 4.0, the integration of MES becomes even more significant, as the interconnected nature of devices and systems allows for improved data utilization.
Overview of MES Functionality
Manufacturing Execution Systems function through several key capabilities. Their primary role includes monitoring production processes, tracking product flows, and facilitating data exchange across various platforms. By offering insights into manufacturing operations, MES empowers decision-makers to optimize workflows and react swiftly to any issues that may arise. This contributes to a more responsive and flexible production environment, aligning with the dynamic demands of today's market.
Components of MES
Data Collection and Monitoring
Data Collection and Monitoring is a fundamental aspect of Manufacturing Execution Systems. This component enables the collection of relevant data from machines, operators, and processes, facilitating a holistic view of the production environment. It is essential for ensuring that operations run smoothly and efficiently. One of the key characteristics of this aspect is the ability to capture accurate, real-time data, which significantly enhances operational decision-making.
One advantage of Data Collection and Monitoring is its ability to identify bottlenecks and inefficiencies early in the production process. However, its reliance on compatible hardware can be a disadvantage, as system integration may present challenges.
Production Tracking
Another vital component of MES is Production Tracking. This function allows manufacturers to follow the journey of a product through the manufacturing process. It provides real-time insights into production statuses, operational performance, and timeline adherence. The key benefit of Production Tracking is its focus on efficiency, allowing for immediate adjustments if targets are not met.
A unique feature of Production Tracking is its capability to connect with various production lines, providing consolidated views that enhance transparency. However, its complexity can present challenges in operation and data interpretation.
Quality Management
Quality Management is an integral part of the MES framework. This aspect ensures that products meet established standards throughout the manufacturing process. By providing tools for inspection and testing, Quality Management supports manufacturers in reducing defects and improving overall product reliability.
The characteristic that sets Quality Management apart is its preventive approach, aiding manufacturers in identifying potential quality issues before they escalate. However, intensive training may be necessary for staff to effectively employ these quality tools, which can require significant resources.
Importance of MES in Manufacturing
The role of MES in manufacturing extends beyond mere oversight; it is key to driving operational effectiveness. With MES, manufacturers can achieve a unified approach to production, leading to increased efficiency and reduced lead times. The collection and analysis of data offer insights that inform strategy and operational improvements.
Furthermore, MES plays a crucial role in enhancing accountability within manufacturing environments. With detailed tracking, organizations can ensure that every product meets quality standards, contributing to customer satisfaction and loyalty. As Industry 4.0 continues to evolve, the importance of MES in fostering innovation and adapting to new challenges cannot be understated.
The Intersection of MES and Industry 4.
The integration of Manufacturing Execution Systems (MES) within the framework of Industry 4.0 plays a pivotal role in re-shaping modern manufacturing. This intersection not only enhances productivity and operational efficiency but also introduces a new paradigm where data-driven decision-making becomes essential. By facilitating real-time data exchange, MES allow manufacturers to respond more swiftly to market dynamics, improving responsiveness to customer needs while maintaining high operational transparency.
Companies leveraging MES within the Industry 4.0 landscape are able to harness the full potential of advanced technologies such as Internet of Things (IoT) and Artificial Intelligence. This synergy drives continuous improvement and empowers organizations to foster a culture of innovation. Therefore, understanding how MES complements Industry 4.0 is crucial for businesses pursuing competitive advantage in today’s fast-evolving industrial ecosystem.
Real-Time Data Exchange
Real-time data exchange is at the heart of how MES operates in an Industry 4.0 environment. By capturing and transmitting data without delays, MES enable instant visibility into production processes. Shops floors equipped with such systems can monitor equipment status, production metrics, and resource allocation in real-time. This leads to immediate issue detection and resolution, thus minimizing downtime.
Through seamless data communication, MES can connect various operational silos, allowing for greater collaboration among teams. It also creates a foundation for predictive analytics, enabling organizations to foresee problems before they arise. As a result, manufacturers can optimize production schedules and react quickly to unforeseen events, enhancing overall resilience.
Enhanced Decision-Making Processes
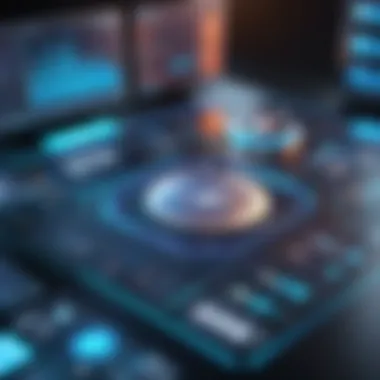
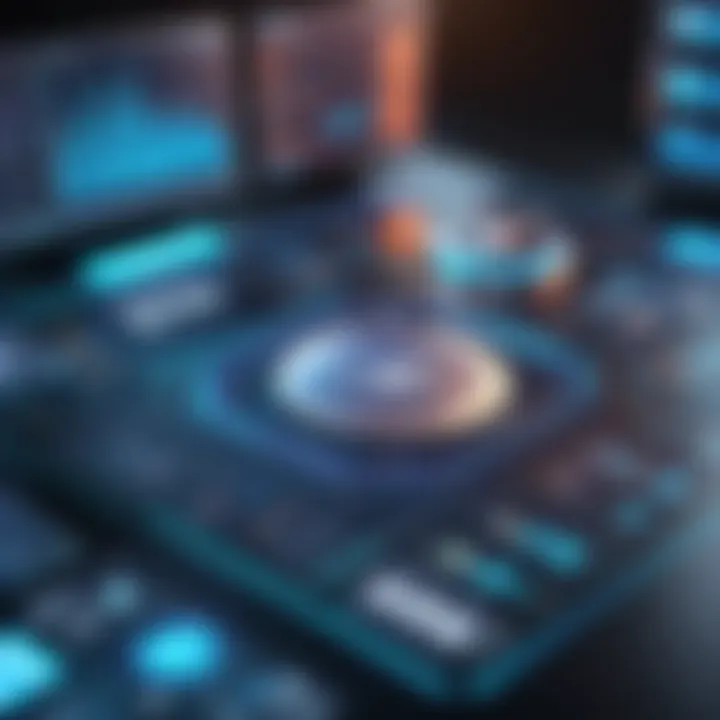
The integration of MES with Industry 4.0 technologies significantly enhances decision-making processes. These systems provide stakeholders with the data they need to make informed decisions quickly, based on current operations and market demands.
Decision-making in manufacturing often involves various dimensions such as quality control, production planning, and inventory management. With accurate, real-time data at hand, managers can assess trends and make adjustments to production plans seamlessly. This responsiveness not only minimizes waste but also supports higher levels of customization to meet unique customer needs. Moreover, predictive models can be employed to forecast production outcomes, allowing managers to take proactive actions.
Integration with Other Systems
The effectiveness of MES in Industry 4.0 is also linked to their ability to integrate efficiently with other technologies and systems. This interconnectedness fosters a cohesive operational framework that drives productivity.
ERP Systems
Enterprise Resource Planning (ERP) systems are critical in facilitating resource management across an organization. Their integration with MES allows for centralized data management, making it easier for firms to align production schedules with supply chain and inventory requirements.
The key characteristic of ERP systems is their comprehensive nature, as they encompass various business functions beyond manufacturing. This makes them a popular choice for organizations looking to streamline operations.
A unique feature of ERP systems is their ability to provide historical data insights that can complement real-time data from MES. This historical context can guide strategic decisions about resource allocation and capacity planning, enhancing operational efficiency. However, the complexity and cost of ERP systems can be a challenge, particularly for smaller businesses.
SCADA Systems
Supervisory Control and Data Acquisition (SCADA) systems are vital for real-time monitoring and control of manufacturing processes. Similar to MES, SCADA systems collect data from various sensors and devices in a manufacturing environment. Their integration with MES enhances data visibility and control.
The key characteristic of SCADA systems is their capability to manage large-scale industrial operations effectively. They provide a real-time operational view, helping organizations maintain control over their processes.
A unique feature of SCADA is its versatility in communication. It can interface with multiple devices and systems, ensuring comprehensive coverage of the production environment. However, some businesses may find SCADA systems to be complex to implement and maintain, requiring specialized knowledge that could be a barrier to entry.
Challenges in Implementing MES
Implementing Manufacturing Execution Systems (MES) within the context of Industry 4.0 is not without its hurdles. These challenges are critical because they can significantly affect the smooth integration of MES into existing manufacturing processes. Overcoming these challenges is essential to harness the full potential of MES and achieve operational excellence. This section examines the prominent challenges faced during the implementation phase: technical barriers, change management issues, and cost implications.
Technical Challenges
The technical challenges of implementing MES mainly stem from the complexities involved in the integration of different technologies. Many legacy systems used in manufacturing environments may not align seamlessly with modern MES solutions. The lack of interoperability between systems can lead to data silos, which is counterproductive to real-time data exchange, a key advantage of MES. Additionally, ensuring data accuracy and robust cybersecurity measures are paramount yet challenging tasks. Organizations must invest in reliable data collection methods to facilitate accurate production tracking and ensure that quality standards are met consistently.
"Integration of MES with existing systems is a tedious but necessary task to gain competitive advantage."
Moreover, companies often face issues related to software scalability. As production demands evolve, the MES must adapt without losing functionality or performance. Failing to establish a clear IT infrastructure or lacking the necessary technical know-how can lead to significant operational disruptions. Addressing these technical challenges is crucial to take advantage of MES capabilities.
Change Management
Change management emerges as another significant challenge in implementing MES. Transitioning to a new system often meets resistance from employees accustomed to existing processes. This can hinder the adoption of MES and lead to problems such as incorrect data entry or improper system use.
Effective change management requires comprehensive training programs and clear communication strategies to convey the benefits of the MES. Employees need to understand not just how to use the system, but also why its implementation is crucial for the organization. Involving staff in the decision-making process can foster a sense of ownership and mitigates resistance.
It is not merely about introducing new technology but also about reshaping corporate culture. If key personnel do not buy into the change, then the chances of successful MES implementation decrease. All stakeholders must be aligned and invested in the outcome for MES to be successful.
Cost Considerations
Cost considerations cannot be overlooked when implementing MES. The financial implications extend beyond initial purchase costs, including ongoing maintenance, training, and potentially costly upgrades in the future. The total cost of ownership must be evaluated before implementation starts.
Investments in MES can yield significant returns through improved efficiency and reduced wastage. However, a detailed cost-benefit analysis is essential to justify the initial expense. Companies must recognize that while the upfront costs might be substantial, the benefits gained in agility, faster decision making, and better quality control can offset these costs over time.
Future Trends in MES and Industry 4.
As industries evolve with the integration of advanced technologies, the role of Manufacturing Execution Systems (MES) becomes increasingly pivotal. Exploring future trends in MES not only highlights how these systems are adapting but also underscores their significance in streamlining processes in Industry 4.0. Companies must position themselves to leverage these trends for competitive advantage and enhanced operational efficiency.
Predictive Analytics Adoption
Predictive analytics stands at the forefront of future trends impacting MES. By harnessing vast quantities of data, predictive analytics enables manufacturers to anticipate equipment failures, optimize maintenance schedules, and improve production efficiency. The value of this technology lies in its ability to convert historical data into actionable insights.
Benefits of predictive analytics include:
- Reduced Downtime: Anticipating issues before they disrupt production.
- Improved Resource Allocation: Better insights into demand patterns help in managing inventory and workforce more effectively.
- Quality Control: By analyzing past production data, companies can mitigate quality issues before they occur.
The Role of Artificial Intelligence
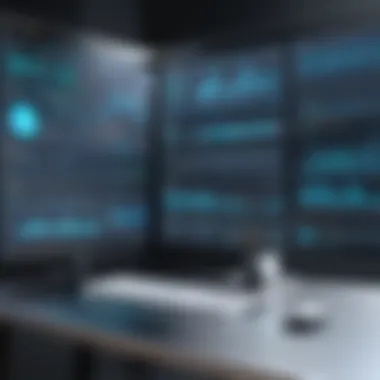
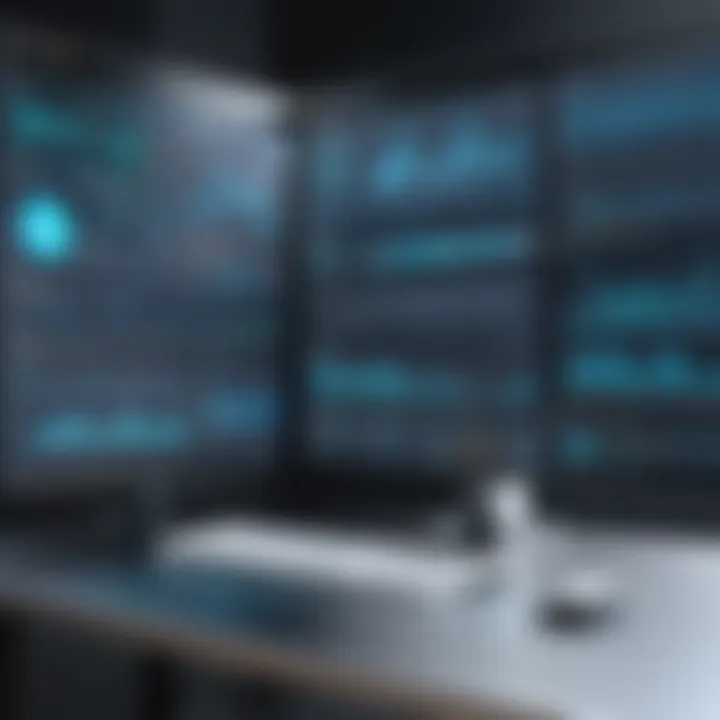
Artificial Intelligence (AI) is revolutionizing the capabilities of MES. Companies are implementing AI-driven systems to enhance decision-making processes. These smart systems analyze real-time data from the production floor and offer recommendations based on machine learning algorithms.
AI applications in MES may include:
- Automated Reporting: AI generates insights that help managers make informed decisions without manual intervention.
- Anomaly Detection: Identifying unusual patterns in performance or quality metrics, allowing for immediate corrective actions.
- Process Optimization: Continuous learning from past operations to suggest improvements in workflows.
Towards Autonomous Manufacturing
The journey towards autonomous manufacturing represents a significant shift in production paradigms. This trend aims to reduce human intervention in manufacturing processes while maintaining a high level of productivity. By integrating advanced technologies, MES can facilitate this transition through increased automation.
Key aspects of autonomous manufacturing include:
- Machine-to-Machine Communication: Systems sharing data autonomously to optimize production lines.
- Self-Optimizing Processes: MES evaluating and adjusting processes based on criteria such as output quality and production speed.
- Scalability: Autonomous systems can easily adapt to changes in production volume, without destabilizing existing operations.
Embracing these future trends will allow businesses to transform their manufacturing processes, driving efficiency and responsiveness in a competitive marketplace.
Case Studies of Successful MES Implementation
Examining successful case studies of Manufacturing Execution Systems (MES) implementation is vital for understanding their impact within various industries. These real-world examples demonstrate how MES can enhance productivity, improve data management, and streamline operations. Insightful case studies reveal the specific elements that contribute to success and highlight the benefits that can be achieved by effectively integrating MES into manufacturing processes. By analyzing these instances, organizations can draw valuable lessons to inform their strategies and decision-making.
Automotive Industry Example
The automotive industry has long been at the forefront of technological advancements. A notable example of MES implementation is Toyota. The company employed a robust MES to monitor production processes in real-time. This allowed for direct tracking of assembly lines, improving efficiency significantly.
Key benefits of Toyota's MES include:
- Real-time visibility of production metrics, resulting in quicker adjustments to workflow.
- Reduction in waste, as the MES identifies bottlenecks and inefficiencies that can be addressed immediately.
- Quality control measures that are enhanced through data analytics, leading to a decrease in defects.
Overall, Toyota’s successful use of MES highlights how crucial real-time data is for maintaining a competitive edge in the automotive sector.
Electronics Manufacturing Example
In the electronics manufacturing sector, Samsung's implementation of MES showcases its effectiveness. The company integrated MES to optimize its production capabilities in semiconductor manufacturing. The MES played a vital role in managing complex production data.
Some of the specific advantages achieved include:
- Improved production efficiency by minimizing downtime through predictive maintenance.
- Enhanced data collection, which allowed for detailed analysis of production patterns and output quality.
- Better inventory management, since the MES linked production schedules to material availability, ensuring a more streamlined operation.
The results demonstrate that MES can handle the intricacies of electronics production, leading to increased output and operational flexibility.
Food and Beverage Industry Example
In the food and beverage industry, Nestlé utilized MES to enhance its manufacturing processes. The company's approach combined traditional methods of food production with cutting-edge MES functionalities. This integration permitted Nestlé to ensure compliance with quality and safety standards across its production lines.
The benefits included:
- Streamlined compliance with regulations, as the MES provided comprehensive traceability of ingredients and processes.
- Increase in production speed due to automated scheduling and clear visibility into production resources.
- Data-driven decision-making, as analytics provided insights into customer trends, allowing for rapid response to market changes.
Nestlé’s case illustrates how MES can be a powerful tool in adhering to stringent industry standards while simultaneously enhancing productivity.
"Case studies of MES implementation offer crucial insights for businesses considering technology investments in their manufacturing processes."
The End
Summarizing Key Insights
The exploration of MES illustrates its fundamental role in bridging the gap between the shop floor and higher management levels. Key takeaways include the following:
- Real-Time Monitoring: MES enables constant tracking of production activities, which is essential for immediate response to issues.
- Data-Driven Decisions: Utilizing data analytics within MES can significantly enhance decision-making capabilities across all levels of production.
- Flexibility and Customization: MES allows for tailored manufacturing processes based on real-time demands, increasing responsiveness to market changes.
- Reduced Waste: By offering insights into production inefficiencies, MES helps in minimizing waste and optimizing resource utilization.
These insights underscore the transformative potential of MES in the manufacturing landscape.
The Path Forward for MES in Industry 4.
As Industry 4.0 continues to evolve, the path forward for Manufacturing Execution Systems is defined by several factors:
- Increased Integration: Future developments will likely focus on deeper integration with other systems, such as Enterprise Resource Planning (ERP) and Scada systems, creating a seamless operational flow.
- Adoption of Advanced Technologies: The use of artificial intelligence and machine learning in MES will enhance predictive capabilities, leading to smarter manufacturing processes.
- Focus on Data Security: With increasing reliance on data, ensuring its security will become paramount. MES will need to adopt robust cybersecurity measures.
- Sustainability Initiatives: Companies will increasingly leverage MES to promote sustainable practices through improved resource management and waste reduction.
In summary, the continued advancement of MES alongside Industry 4.0 technologies presents a compelling case for organizations focused on remaining competitive. Emphasizing data-centric approaches and prioritizing integration will be key to unlocking the full potential of these systems in the manufacturing domain.